How Do You Not Stick When Welding => To avoid sticking when welding, maintain the proper arc distance between the electrode tip and the base metal. Ensure that you are running the arc at the correct length and with enough amperage.
Practice and experimentation will help improve your technique and prevent sticking. It is important to find your balance and stability while welding, and getting your hands as close to the arc as possible will help achieve this. Resting your hands or arms against a solid surface can also provide stability.
Remember to dial in the appropriate amperage for your project to avoid sticking. Proper technique and amperage will help prevent your stick from getting stuck when welding.
Understanding Stick Welding Basics
Definition and Overview of Stick Welding
Stick welding, also known as shielded metal arc welding (SMAW), is a popular welding technique that involves using an electrode and an electric-based welding machine to create a strong bond between metals. This process is widely used in various industries, including construction, automotive, and metal fabrication.
Explanation of the Welding Arc and Electrode
During stick welding, the welding arc is formed between the electrode and the base metal. The electrode, which is usually coated with flux, serves as a consumable filler material. It produces heat and creates a molten pool that solidifies to form a solid joint when it cools down.
The welding arc acts as a heat source and melts both the electrode and the base metal to create a strong bond. The arc is created when the electrode is brought into contact with the base metal and then pulled away slightly to establish a controlled gap, known as the arc length.
Importance of Maintaining Proper Arc Length
One of the key factors in preventing the electrode from sticking to the metal during stick welding is maintaining the proper arc length. The arc length is the distance between the electrode tip and the base metal.
If the arc length is too short, the electrode may stick to the metal due to excessive heat and lack of sufficient arc force. On the other hand, if the arc length is too long, the arc may become unstable, making it difficult to control the welding process.
It is crucial to maintain a consistent and proper arc length throughout the welding process to ensure a successful weld. This can be achieved by adjusting the distance between the electrode and the base metal according to the type of electrode, welding position, and desired weld quality.
In addition to maintaining proper arc length, other factors such as amperage, electrode angle, and travel speed also play important roles in preventing electrode sticking. With practice and experience, welders can develop the skills needed to control these variables and achieve optimal welding results.
By understanding the basics of stick welding, including the definition and overview of stick welding, the mechanisms of the welding arc and electrode, and the importance of maintaining proper arc length, welders can improve their skills and avoid electrode sticking during the welding process.
Factors That Contribute To Sticking
When it comes to welding, sticking can be a frustrating problem that can hinder the welding process. Various factors can contribute to sticking during welding, and understanding these factors is crucial to avoid this issue and achieve successful welds. Below, we discuss two major factors that commonly contribute to sticking: insufficient amperage and short arc length, and problems with electrode positioning and overall technique.
Insufficient Amperage and Short Arc Length
One of the main reasons for sticking during welding is insufficient amperage and a short arc length. If the amperage is too low, there won’t be enough current flowing through the electrode, resulting in a weak and unstable arc. This can cause the electrode to stick to the base metal, making it difficult to strike and maintain the arc.
Additionally, a short arc length can also lead to sticking. When the arc length is too short, the electrode comes into close contact with the base metal, increasing the likelihood of it sticking. It’s important to maintain an appropriate arc length, where there is enough space between the electrode tip and the base metal to allow for a stable arc and prevent sticking.
Problems with Electrode Positioning and Overall Technique
Another factor that can contribute to sticking during welding is problems with electrode positioning and overall technique. Improper electrode positioning can lead to sticking as the electrode may make improper contact with the base metal or get too close to the weld pool. It’s important to ensure that the electrode is positioned correctly and at the right angle to achieve a smooth and stable arc.
Furthermore, overall welding technique plays a crucial role in preventing sticking. Welding requires steady hands and controlled movement to maintain a stable arc. If the welder’s hands are shaky or the movement is erratic, the electrode may stick to the base metal. Taking the time to practice and improve overall welding technique can help prevent sticking and achieve better welds.
In conclusion, when it comes to welding, factors such as insufficient amperage and short arc length, along with problems with electrode positioning and overall technique, can contribute to sticking. By understanding and addressing these factors, welders can avoid sticking issues and achieve successful welds.
Tips For Avoiding Sticking
Hot start technique for easier arc initiation
The hot start technique is a useful method for ensuring easier arc initiation and avoiding sticking while welding. It involves preheating the electrode by briefly touching it to the base metal before starting the arc. This helps to establish a smoother arc and reduces the chances of the electrode sticking to the metal.
Familiarizing yourself with your welding machine
To avoid sticking while welding, it’s important to become familiar with your welding machine. Understanding its settings, controls, and capabilities will enable you to adjust the parameters according to your specific welding needs. Pay attention to factors such as amperage settings, electrode type, and proper polarity to ensure a smooth and efficient welding process.
Regular practice to improve welding skills
Like any skill, welding requires regular practice to improve proficiency and minimize the chances of sticking. Set aside dedicated practice sessions to enhance your welding technique and become more comfortable with the process. Regular practice will help you develop a consistent and steady hand, making it easier to maintain the correct arc length and prevent sticking.
Here are some additional tips to keep in mind when welding:
- Always use the appropriate welding rod for the type of metal you are welding.
- Maintain the correct arc length by adjusting the distance between the electrode and the base metal.
- Ensure proper grounding to avoid electrical shock hazards.
- Monitor your amperage to ensure it is sufficient for the material being welded.
- Control your travel speed to maintain a steady and even bead.
By implementing these tips and continuously honing your welding skills through regular practice, you can minimize the chances of sticking and achieve clean and strong welds.
Resolving Sticking Issues
Resolving Sticking Issues:
When it comes to stick welding, one of the most common challenges that welders face is sticking. This occurs when the electrode gets stuck to the metal surface, making it difficult to move smoothly. However, there are ways to resolve sticking issues and ensure a more seamless welding experience.
Methods for restarting a stuck electrode
If you find your electrode sticking to the metal, don’t panic. There are several methods for restarting a stuck electrode that can help you get back on track:
- Tap Method: The tap method is an effective way to break the arc and remove the stickiness. Simply tap the electrode on a hard surface to break the connection with the metal. This allows you to reposition the electrode and continue welding without sticking issues.
Understanding the specifications of welding rods
To prevent sticking issues, it is crucial to understand the specifications of the welding rods you are using. Each welding rod has its own characteristics and requirements, so it’s essential to choose the right one for your specific welding project. Here are some key specifications to consider:
Specification | Description |
---|---|
Diameter | The diameter of the welding rod can affect the arc stability. Using the correct diameter for your welding machine can help prevent sticking issues. |
Amperage Range | Each welding rod has an optimal amperage range for best results. If the amperage is too low, the electrode may stick to the metal. Adjusting the amperage within the recommended range can help avoid sticking. |
Coating Type | The coating on the welding rod can also impact the welding process. Different coatings provide different characteristics, such as easier arc ignition and reduced sticking. Understanding the coating type can help you choose the right rod for your welding needs. |
By properly understanding and considering these specifications, you can ensure that your welding rods are compatible with your welding technique and avoid sticking issues.
In conclusion, resolving sticking issues is crucial for a smooth and effective welding process. By employing methods such as the tap method to break the arc and understanding the specifications of welding rods, you can minimize sticking and achieve better welding results. So, keep these tips in mind and weld with confidence!
How To Prevent Electrode Stickiness
Exploring the reasons behind electrodes sticking to metal
When it comes to welding, electrode stickiness can be a common issue that many welders face. There are several reasons why electrodes stick to metal during the welding process. One of the main reasons is the improper maintenance of the arc distance between the electrode tip and the base metal.
If the arc distance is too short, it can lead to the electrode sticking to the metal, making it difficult to weld smoothly. Another reason for electrode stickiness can be insufficient amperage, which can also result in a sticky arc.
To prevent electrode sticking, it is important to maintain the proper arc distance and ensure adequate amperage. By understanding the reasons behind electrode sticking, welders can take the necessary steps to prevent this issue and improve their welding results.
Importance of maintaining proper arc distance
Maintaining the proper arc distance is crucial for successful and efficient welding. The arc distance refers to the space between the electrode tip and the base metal. When the arc distance is too short, the electrode can stick to the metal, causing disruptions in the welding process.
On the other hand, if the arc distance is too long, it can result in an unstable arc that splatters and creates a weak weld. By maintaining the ideal arc distance, welders can achieve a stable and controlled arc, ensuring proper fusion and deposition of the filler metal. This not only improves the quality of the weld but also reduces the likelihood of electrode stickiness.
To maintain the correct arc distance, welders should refer to the manufacturer’s recommendations for the specific electrode and welding technique being used. Regular practice and experience also play a crucial role in mastering the art of maintaining proper arc distance.
Troubleshooting tips for controlling arc length
Controlling the arc length is essential for preventing electrode stickiness and achieving consistent and high-quality welds. Here are some troubleshooting tips to control arc length effectively:
1. **Adjusting amperage:** One of the main factors that affect arc length is the amperage setting. If the amperage is too low, it can result in a shorter arc and increased chances of electrode sticking. Increasing the amperage to the appropriate level can help maintain a stable arc with the ideal length.
2. **Choosing the right electrode:** Different electrodes have different characteristics and requirements when it comes to arc length. It is important to select the appropriate electrode for the specific welding application to ensure better control over the arc length. Consult the electrode manufacturer’s specifications for guidance.
3. **Maintaining a steady hand:** Welders should focus on keeping their hands as close to the welding arc as possible. This helps in achieving better stability and control over the arc length. Resting the hands or arms against a solid surface can also improve steadiness during the welding process.
4. **Using proper welding technique:** Mastering proper welding techniques, such as maintaining a consistent travel speed and angle, can contribute to controlling the arc length effectively. Practice and experience play a significant role in developing the skills required for optimal arc control.
By following these troubleshooting tips and practicing proper welding techniques, welders can overcome the challenges associated with controlling arc length and significantly reduce the occurrence of electrode stickiness during the welding process. Remember, patience and practice are key to becoming a skilled welder capable of producing high-quality welds.
Common Mistakes To Avoid
Not using the correct welding rod for the job
One of the most common mistakes that beginners make when welding is not using the correct welding rod for the job. Each type of welding rod is designed for specific purposes and materials. Using the wrong type of rod can result in sticking, poor weld quality, and even damage to the material being welded.
Make sure you choose the right welding rod by considering factors such as the type of metal you are working with, the thickness of the material, and the welding technique you will be using. It is important to consult with a welding expert or refer to the manufacturer’s guidelines for the correct welding rod selection.
Poor electrode control and positioning
Another mistake that can lead to sticking during welding is poor electrode control and positioning. When welding, it is crucial to maintain a steady hand and proper electrode positioning to achieve high-quality welds.
Ensure that your hand is stable and your grip on the electrode is firm but not too tight. Avoid excessive movement or shaking of your hand during the welding process. This can cause the electrode to deviate from the desired welding path and result in sticking or inconsistent welds.
Additionally, pay attention to the proper angle and distance between the electrode and the workpiece. Improper positioning can cause the electrode to stick or create weak welds.
Lack of steady hand and overall stability
One of the most important factors in avoiding sticking when welding is maintaining a steady hand and overall stability. Welding requires precision and control, and any excessive movement can lead to sticking or poor weld quality.
To improve your stability, try to find a comfortable position that allows you to rest your hands or arms against a solid surface, such as a welding table or a support stand. This will help minimize hand tremors and ensure better control of the electrode.
Additionally, practice proper body posture and balance. Stand with your feet shoulder-width apart and distribute your weight evenly. This will help you maintain stability and prevent unnecessary movement during the welding process.
Other Types Of Arc Welding
Overview of Shielded Metal Arc Welding (SMAW)
In the realm of arc welding, shielded metal arc welding (SMAW), also known as stick welding, is a widely practiced technique. The process involves the use of a consumable stick electrode that is coated with flux, creating a protective shield around the weld.
This shield prevents the weld from being contaminated by atmospheric gases, ensuring a strong and durable bond. SMAW is highly versatile and can be used on various materials, making it a preferred choice for many welders.
One of the key aspects to keep in mind when practicing SMAW is maintaining the proper arc length. The distance between the electrode tip and the base metal plays a crucial role in preventing sticking during the welding process. By ensuring the correct arc length, you can control the heat input and achieve optimal weld penetration without causing the electrode to stick to the metal.
Introduction to Gas Metal Arc Welding (GMAW)
Gas metal arc welding (GMAW), commonly referred to as MIG welding, utilizes a continuous wire electrode and a shielding gas to protect the weld. It is known for its efficiency and speed, making it a popular choice in industries where high productivity is required. GMAW offers excellent control over the welding process, allowing welders to achieve precise and clean welds.
When it comes to preventing sticking during GMAW, the key lies in maintaining proper wire feed speed and amperage settings. By adjusting these parameters according to the specific material and joint being welded, welders can ensure smooth wire transfer and prevent the electrode from sticking to the workpiece.
Brief Explanation of Gas Tungsten Arc Welding (GTAW)
Gas tungsten arc welding (GTAW), also known as TIG welding, is a precise and versatile welding technique that is commonly used for thin materials and intricate welds. GTAW utilizes a non-consumable tungsten electrode, along with a shielding gas, to protect the weld and create a strong bond.
In GTAW, preventing sticking largely involves maintaining a steady hand and precise control over the welding parameters. By employing techniques such as proper electrode angle and manipulation, welders can prevent the electrode from sticking to the workpiece.
In conclusion, each type of arc welding comes with its own set of challenges when it comes to preventing sticking. Whether it’s SMAW, GMAW, or GTAW, proper technique, control over welding parameters, and a steady hand are essential in achieving optimal results and avoiding electrode sticking. By mastering these skills and understanding the nuances of each welding process, welders can elevate their craft and create high-quality, durable welds.
Faqs
Why do welders not get shocked while welding?
Welders do not get shocked while welding because the voltages used for welding are just a few volts. At this potential, your skin acts as a good enough insulator to prevent a current from flowing, which would be large enough for you to sense as a shock. So, even though welding involves electricity, the low voltage used doesn’t pose a risk of electric shock.
Source: Engineering Stack Exchange
Why is stick welding considered challenging?
Stick welding is considered challenging for a few reasons. Firstly, if you don’t have a high enough amperage, the electrode becomes stickier, making it difficult to strike an arc without getting stuck to the metal. Insufficient amperage also means there’s not enough heat to melt the core wire, making it harder to achieve a proper weld.
Source: Quora
How can I prevent my stick from getting stuck in the metal?
To prevent your stick from getting stuck in the metal while stick welding, there are a few tips you can follow:
- Ensure you maintain proper arc distance between the electrode tip and the base metal. Running your arc too short or using too little amperage can cause the stick to get stuck.
- Practice your technique regularly to improve your control over the welding process.
- Pay attention to the type of flux used, as using the right flux can help prevent sticking.
- If your stick does get stuck, using a tapping method with a hammer can help release it from the metal.
- Finally, familiarize yourself with the welding rod specifications you are using. Different rods have different properties and using the right one for your specific application can help minimize sticking.
Source: Weld.com YouTube
Source: TimWelds YouTube
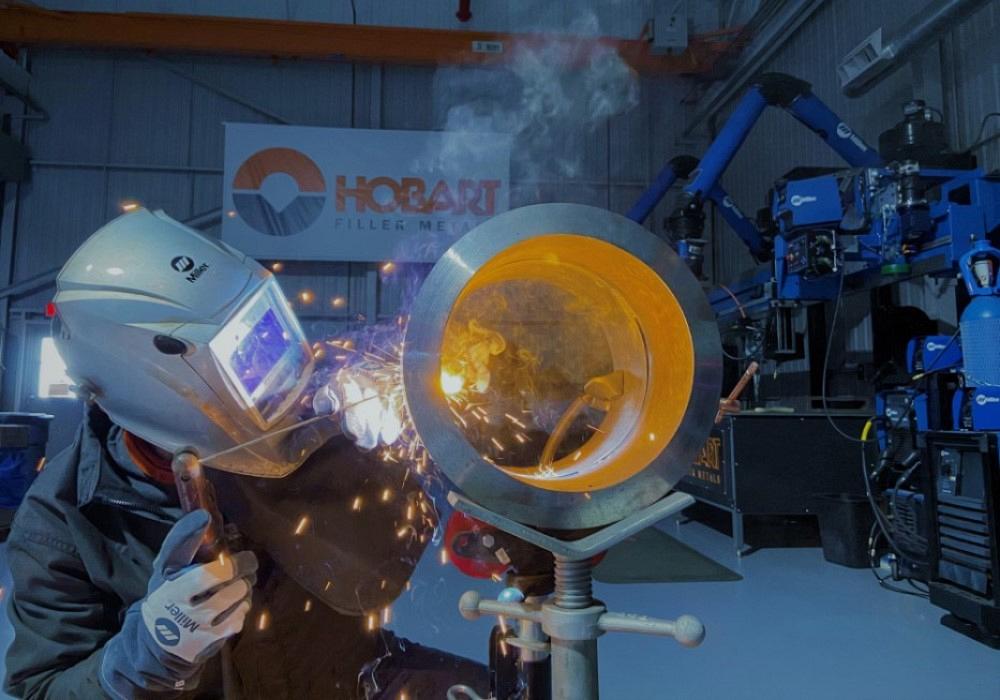
Credit: www.thefabricator.com
Frequently Asked Questions Of How Do You Not Stick When Welding?
Why Does My Stick Get Stuck When I Weld?
Your stick gets stuck when you weld because you may not be maintaining the proper arc distance between the electrode tip and the base metal. This can be due to running your arc too short or using too little amperage.
Keep practicing and you’ll improve your technique.
How Do Welders Not Get Shocked?
Welders do not get shocked because the voltages used for welding are low, preventing a current strong enough to cause a shock. Proper technique, including maintaining the right arc distance and using the correct amperage, also helps prevent sticking. Being stable during welding by getting closer to the arc or resting against a solid surface can improve welding quality.
Why Is Stick Welding So Hard?
Stick welding can be difficult because of the need to maintain the proper arc distance between the electrode tip and the base metal. If the arc is too short or if there is not enough amperage, the electrode can stick to the metal, making it hard to strike an arc.
Practice and proper technique can help overcome this challenge.
How Can I Be More Stable When Welding?
To be more stable when welding, follow these tips: 1. Get as close to the arc as possible. 2. Rest your hands or arms against a solid surface for support. 3. Maintain proper arc distance between the electrode tip and base metal.
4. Practice controlling arc length and maintaining a steady hand. 5. Increase amperage for better control and to prevent sticking. By implementing these techniques, you can achieve greater stability during welding.
How Can I Prevent Sticking When Welding?
To prevent sticking when welding, maintain a proper arc distance between the electrode tip and the base metal. Practice running your arc with the correct length and amperage.
Conclusion
To avoid sticking when welding, it is crucial to maintain the proper arc distance between the electrode tip and the base metal. By running the arc too short or using too little amperage, the electrode can get stuck. However, with practice and the right technique, this issue can be overcome.
Welders can also improve stability by getting closer to the arc and resting their hands or arms against a solid surface. By following these tips, welders can achieve smooth and successful welds without experiencing sticking.