When stick welding, the angle at which you hold the electrode is crucial for achieving a good weld. Generally, a 45-degree angle is recommended for stick welding.
This angle allows for better penetration and control of the welding arc. However, it’s important to note that the optimal angle may vary depending on the thickness of the materials being welded and the position of the weld. It’s always a good idea to consult welding reference guides or seek advice from experienced welders to determine the best angle for your specific welding project.
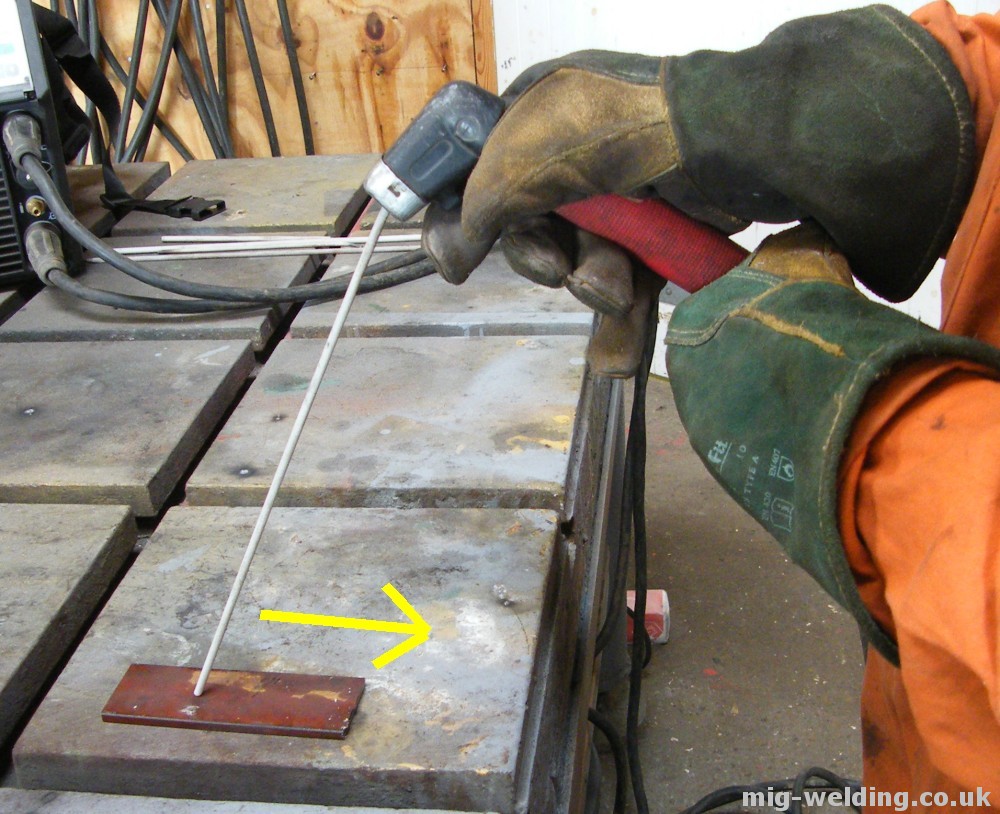
Credit: www.mig-welding.co.uk
Understanding The Importance Of Angles In Stick Welding
Introduction To Stick Welding Angles
In stick welding, understanding the importance of angles is crucial to achieving high-quality welds with proper penetration. The angle at which you hold the welding electrode, known as the rod angle, plays a significant role in determining the strength and integrity of your welds.
By mastering the correct angles, you can ensure better control, consistent weld deposits, and improved overall welding performance.
The Impact Of Angle On Weld Quality And Penetration
The angle at which you hold the welding electrode directly affects both the quality and penetration of your welds. It determines how the heat and filler material are distributed, ultimately influencing the durability and strength of the weld. Let’s explore how different welding angles can impact your welds:
1. Vertical (Upward) Angle
A vertical upward welding angle, where you tilt the electrode in an upward direction between 0 to 15 degrees, is ideal for achieving deep penetration. This technique is commonly used when welding thicker materials or performing joints that require strong welds. The vertical angle allows the heat to concentrate towards the base metal, resulting in excellent fusion and weld strength.
2. Vertical (Downward) Angle
A vertical downward welding angle, where you tilt the electrode in a downward direction between 0 to 15 degrees, is preferred for thinner materials. While this angle may provide less penetration compared to the upward angle, it enables faster welding speeds. It is essential to maintain control and regulate the heat input to prevent burn-through or insufficient fusion.
3. Horizontal Angle
The horizontal welding angle, also known as the drag angle, involves holding the electrode horizontally or parallel to the joint. This angle is commonly used for fillet welds and flat-position welding.
It provides good control over the weld pool, allowing for smooth and consistent bead formation. The horizontal angle is suitable for achieving adequate fusion and maintaining uniform sidewall fusion.
4. Overhead Angle
The overhead welding angle requires welding in an overhead position, such as welding on the underside of a joint. It demands precision and skill to ensure proper penetration and complete fusion. It is crucial to position yourself correctly and pay attention to the molten weld pool to achieve sound and high-quality overhead welds.
Remember, mastering the proper welding angle is essential, but it is equally important to consider other factors such as welding speed, electrical settings, and hand movement. Experimenting with different angles and practicing various techniques will help you develop your skills and improve the overall quality of your stick welding.
For more in-depth information and guidance on stick welding angles, please refer to the following resources:
- Key Rules on Welding Angle, Direction, and Speed
- Five Steps to Improving Your Stick Welding Technique
- Stick Welding Tips To Sincerely Improve Your Work – Cruxweld
- Basic Stick Welding – Electrode Technique
- The Ultimate Guide to STICK Welding (UNIMIG)
The Optimum Angle For Stick Welding
Determining The Ideal Angle For Stick Welding
When it comes to stick welding, determining the ideal angle is crucial for producing high-quality welds. The angle at which you hold the electrode can significantly affect the weld penetration, bead shape, and overall quality of the weld. In this section, we will explore the key factors to consider when choosing the angle as well as recommended angles for different welding positions.
Factors To Consider When Choosing The Angle
Choosing the right angle for stick welding depends on various factors, including the type of electrode, welding position, joint configuration, and base metal thickness. Here are the key factors to consider:
- Electrode type: Different electrode types have specific angle recommendations. For example, a typical angle for a stick welder using E6010 or E6011 electrodes is around 15 degrees.
- Welding position: The welding position determines how you position the electrode about the joint. In the flat and horizontal positions, a drag or slightly backhand technique is commonly used, where the angle is typically between 5 to 15 degrees. In vertical and overhead positions, a push or slightly forehand technique is preferred, with angles ranging from 5 to 15 degrees.
- Base metal thickness: Thicker materials generally require a steeper electrode angle to ensure adequate penetration, while thinner materials may benefit from a shallower angle to prevent excessive heat build-up and burn-through.
Recommended Angles For Different Welding Positions
Here are the recommended angles for stick welding in different positions:
Welding Position | Recommended Angle |
---|---|
Flat & Horizontal | 5° to 15° (drag or slightly backhand technique) |
Vertical | 5° to 15° (push or slightly forehand technique) |
Overhead | 5° to 15° (push or slightly forehand technique) |
It’s worth noting that these recommended angles serve as a starting point and may need to be adjusted based on specific circumstances and personal preferences. The goal is to achieve proper weld penetration, control the heat input, and create a well-formed bead.
By considering the factors mentioned above and practicing with different angles, you can develop a better understanding of how the electrode angle affects the weld quality and make informed decisions while stick welding.
Techniques For Stick Welding At Different Angles
Flat Position Stick Welding Techniques
When stick welding in a flat position, it is important to maintain a consistent arc length and travel speed. This position allows for easier control and manipulation of the electrode, resulting in cleaner and more precise welds.
Here are some key techniques for stick welding in the flat position:
- Drag angle: Holding the electrode at a slight drag angle of around 15-20 degrees helps in maintaining proper arc length and depositing a consistent bead.
- Weaving motion: Utilizing a side-to-side weaving motion while welding helps in distributing the heat evenly across the joint and prevents overheating in one specific area.
- Slow travel speed: Moving the electrode slowly along the joint allows for better fusion and penetration, resulting in stronger welds.
- Maintain a steady hand: Keeping a steady hand while stick welding in the flat position is crucial for smooth and consistent bead formation.
Horizontal Position Stick Welding Techniques
Stick welding in the horizontal position requires some adjustments to maintain proper penetration and prevent weld drooping. Here are some techniques to keep in mind:
- Uphill welding: When stick welding in the horizontal position, welding uphill is generally preferred as it provides better penetration and a stronger weld. Uphill welding involves dragging the electrode upwards along the joint.
- Angle adjustment: Adjusting the angle of the electrode slightly toward the direction of travel helps in maintaining the proper weld profile and preventing excess weld material from sagging or spreading too wide.
- Weaving motion: Utilizing a controlled weaving motion while stick welding horizontally helps in distributing the heat evenly and ensures proper fusion along the joint.
- Overlap technique: Overlapping the weld beads slightly helps in achieving a wider weld and creating a continuous and strong joint.
Vertical Position Stick Welding Techniques
Stick welding in the vertical position can be challenging due to gravity pulling the molten metal downwards. However, with the right techniques, quality welds can be achieved in this position. Here are some crucial techniques for stick welding vertically:
- Upward welding: Welding from bottom to top, known as upward welding, is the most common technique in the vertical position. This technique allows you to control the weld pool and prevents excessive sagging.
- Tight arc: Keeping a tight arc length of around 1/8 inch helps maintain the proper heat input and prevents excessive overheating.
- Tacking: Tacking the joint at intervals helps in stabilizing the weld and prevents it from sliding down due to gravity.
- Weaving motion: Utilizing a controlled weaving motion while stick welding vertically helps in evenly distributing the heat and ensures proper fusion along the joint.
Overhead Position Stick Welding Techniques
Stick welding in the overhead position is considered the most challenging due to gravity pulling the molten metal downwards. It requires precision and control to produce quality welds. Here are some techniques for stick welding overhead:
- Short arc length: Using a shorter arc length helps reduce the chances of excessive drooping or sagging of the weld bead.
- Angle adjustment: Adjusting the angle of the electrode slightly toward the direction of travel helps maintain the proper weld profile and prevents excess weld material from sagging or spreading too wide.
- Weaving motion: Employing a tight and controlled weaving motion while stick welding overhead helps in evenly distributing the heat and ensures proper fusion along the joint.
- Reduced amperage: Lowering the amperage slightly compared to other positions can help in better control and prevent excessive melting or burning of the base metal.
Common Mistakes To Avoid When Stick Welding At Different Angles
Stick welding is a versatile and widely used welding technique that involves joining metal pieces using an electric arc. One crucial factor that can greatly affect the quality and strength of the weld is the angle at which the electrode is held.
Many welders overlook the importance of angle and end up making common mistakes that compromise the weld quality. In this section, we will explore some of these mistakes and highlight the consequences they can have.
Incorrect Electrode Angle And Its Consequences
The angle at which the electrode is held during stick welding plays a vital role in determining the quality and penetration of the weld. One common mistake is to hold the electrode too perpendicular to the workpiece, resulting in an improper electrode angle. This can lead to several consequences:
- Poor penetration: Holding the electrode too perpendicular can cause a lack of penetration, leading to weak and unreliable welds.
- Inadequate fusion: Improper electrode angle can also result in insufficient fusion between the base metal and the electrode, compromising the overall integrity of the weld.
- Excessive spatter: Holding the electrode at the wrong angle can increase the amount of spatter produced during the welding process. This not only creates a messy work environment but also affects the weld appearance and quality.
Compromising Weld Quality Due To Improper Angle
Another common mistake made by welders is compromising the weld quality due to improper angle selection. This often happens when welders prioritize convenience over achieving the optimal angle for the specific welding joint.
Some consequences of compromising weld quality due to improper angle include:
- Weakened joints: Using incorrect angles can result in weakened weld joints, reducing the overall strength and structural integrity of the finished product.
- Inconsistent welds: Incorrect angle selection can lead to inconsistent welds, with variations in bead size, depth, and quality across the weld joint. This can compromise the overall aesthetics and functionality of the weld.
- Increased rework and waste: When the angle is not optimized, welders may need to spend additional time and effort on rework to fix weak or inadequate welds. This not only leads to increased labor costs but also generates more scrap metal waste.
To ensure high-quality stick welds, it is crucial to avoid the common mistakes associated with angle selection. By paying attention to electrode angle and choosing the optimal angle for each welding joint, welders can achieve strong, reliable, and visually appealing welds.
Tips For Maintaining Consistency In Stick Welding Angles
Stick welding, also known as shielded metal arc welding (SMAW), is a popular welding method due to its versatility and ease of use. One crucial aspect of stick welding is maintaining consistent welding angles, which greatly affects the quality of the weld and the overall strength of the joint. In this section, we will discuss some essential tips for maintaining consistency in stick welding angles.
Practicing And Developing A Steady Hand For Angle Control
When it comes to stick welding, maintaining a steady hand and precise angle control is vital for producing high-quality welds. To develop a steady hand, it is necessary to practice regularly and refine your technique. Here are a few techniques to help you improve angle control:
- Maintain proper body positioning: Stand with your feet shoulder-width apart, ensuring a stable base. Keep your torch hand steady and close to your body for more control.
- Support your hand: If possible, rest your hand on a solid surface or use a steady rest to stabilize your welding hand. This will help minimize hand tremors and improve angle consistency.
- Utilize finger control: Use your fingers to control the torch movement and maintain a consistent angle. Practice precise finger movements to ensure accuracy and uniformity in your welds.
Using Visual Aids And Fixtures To Ensure Consistent Angles
Visual aids and fixtures can be highly beneficial in maintaining consistent welding angles throughout your project. Here are some strategies to consider:
- Angle guides: Attach angle guides or magnets to your workpiece to provide a visual reference for maintaining the desired angle. These guides can help reduce the chances of veering off course and ensure consistency.
- Welding jigs and fixtures: Implementing welding jigs and fixtures can assist in holding your workpiece at a specific angle, making it easier to maintain consistency. These tools can be especially helpful when working with complex or irregularly shaped parts.
- Use templates: Create templates or cutouts of the desired angle to visually guide your torch hand. These templates can serve as a reference point to ensure accurate angle positioning.
Regularly Checking And Adjusting Electrode Angles During Welding
During stick welding, it is crucial to check and adjust the electrode angle periodically to maintain consistency and produce high-quality welds. Here are some key points to remember:
- Create a consistent drag angle: For most stick welding applications, a slight drag angle is recommended. This means keeping the electrode tilted back in the direction of travel, typically around 5-15 degrees.
- Monitor the electrode angle: Continuously observe the angle of the electrode during welding. Be sure to make small adjustments as needed to maintain the correct drag angle and prevent excessive electrode stubbing.
- Develop a feel for the arc: With practice, you will develop a sense of the correct angle based on the sound and the appearance of the arc. This will help you make real-time adjustments and maintain consistency throughout the welding process.
Maintaining consistent angles in stick welding is crucial for achieving strong and visually appealing welds. Remember to practice and develop a steady hand, utilize visual aids and fixtures, and regularly monitor and adjust the electrode angle. By implementing these tips, you can enhance the quality of your stick welding projects and produce professional-level results.
Troubleshooting Common Issues Related To Stick Welding Angles
Weld Bead Irregularities Caused By Improper Angle
One of the most common issues that can arise from improper stick welding angles is weld bead irregularities. When the angle is too steep or too shallow, it can result in an uneven and inconsistent weld bead. This can lead to weaker welds and potential structural problems. It is crucial to find the right angle that allows the electrode to establish a stable arc while ensuring proper fusion and penetration.
Here are some of the weld bead irregularities that can occur due to improper angle:
- Inconsistent bead width
- Undercutting
- Overlap
- Underfill
When troubleshooting these issues, check your angle and make sure it is optimized for the specific weld joint and position. Adjusting the angle can help achieve a more uniform and aesthetically pleasing weld bead.
Insufficient Penetration Due To Incorrect Angle
Proper penetration is essential for a strong and durable stick weld. Inadequate penetration can result from using an incorrect angle. When the angle is too shallow, the electrode may skim the surface without fully penetrating the base metal, leading to weak and unreliable welds.
Some signs of insufficient penetration include:
- Lack of fusion
- Cracks or incomplete joint penetration
- Poor bead profile
To troubleshoot insufficient penetration, consider adjusting the angle to achieve better heat control and deeper penetration. Experiment with different angles and observe the changes in weld quality and penetration.
Overheating And Distortion Caused By Excessive Angle
While insufficient angle can lead to weak welds, excessive angle can result in overheating and distortion. When the angle is too steep, the concentrated heat can cause the base metal to overheat, leading to unwanted distortion and warping.
Here are some potential issues caused by excessive angle:
- Burn-through
- Excessive spatter
- Distorted weld joint
To troubleshoot overheating and distortion, try adjusting the angle to a shallower position. This will help distribute the heat more evenly and reduce the concentration of heat in a specific area.
Frequently Asked Questions Of What Angle Should I Stick Weld At?
Do You Push Or Pull When Stick Welding?
In stick welding, it is recommended to push the electrode rather than pull it. Pushing allows for better control of the arc and helps in achieving a smoother and more stable weld.
Are You Supposed To Weld Uphill Or Downhill?
For stick welding, both uphill and downhill methods have their advantages. Uphill welding is preferred for higher quality and better penetration in thicker materials, while downhill is faster and more suitable for thinner materials.
What Angle Should I Hold The Stick Welder At?
Hold the stick welder at a 10-degree angle for the best results.
Should I Push Or Pull When Stick Welding?
For stick welding, it is generally better to push the electrode along the joint for smoother welds.
Is It Better To Weld Uphill Or Downhill?
Both methods have their advantages, but welding uphill is generally preferred for better penetration, especially in thicker materials.
Conclusion
To achieve optimal stick welding results, it is important to consider the angle at which you weld. While there is no one-size-fits-all answer, a general rule of thumb is to position the electrode at a 45-degree angle in the direction of travel.
This angle provides good arc control and penetration. However, it is essential to remember that factors such as material thickness and joint configuration may require adjustments to the angle. By experimenting with different angles and fine-tuning your technique, you can achieve high-quality and structurally sound welds.
Keep practicing and refining your skills to become a master in stick welding.