The quickest welding type is MIG welding, which is known for its high productivity and easy learning curve. MIG welding uses a feed wire that runs through the machine at a preselected speed, making it a fast and efficient process that produces consistent welds.
This type of welding is especially beneficial for beginners, as it is easy to learn and operate. Additionally, MIG welding can be used on flux-cored welding projects, adding to its versatility and speed. Overall, MIG welding is the fastest welding technique, offering fast results and high productivity.
What Is Welding?
The quickest welding type is MIG welding, which is known for its high productivity and ease of use. MIG welding uses a feed wire that runs through the machine at a preselected speed, making the process fast and producing consistent welds.
Welding is the process of joining two or more pieces of metal together using heat and pressure. It involves the melting and fusing of the metals to create a strong bond. Welding is essential in various industries, including construction, manufacturing, automotive, and aerospace.
Here are some key points to understand about welding:
- Definition and explanation of welding:
- Welding is a fabrication process that involves the fusion of materials, commonly metals, to form a strong joint.
- The process typically requires the use of heat, pressure, or both to melt and join the materials together.
- The goal of welding is to create a permanent bond that is as strong as the base materials being joined.
Importance And Applications Of Welding In Various Industries:
- Construction industry:
- Welding is crucial in the construction industry for joining structural steel components, fabricating bridges, and constructing buildings.
- It helps create sturdy and durable structures that can withstand various environmental conditions.
- Manufacturing industry:
- Welding plays a vital role in the manufacturing sector for assembling different metal components, such as machinery, equipment, and vehicles.
- It ensures the integrity and functionality of the manufactured products.
- Automotive industry:
- Welding is extensively used in the automotive industry for joining metal parts during the manufacturing process.
- It helps in the construction of vehicle frames, body panels, exhaust systems, and engine components.
- Aerospace industry:
- Welding is critical in the aerospace industry for manufacturing aircraft components and structures.
- It ensures the structural integrity and safety of aircraft.
- Other industries:
- Welding also finds application in various other industries, including shipbuilding, oil and gas, pipelines, power plants, and infrastructure development.
Welding is the process of joining metals together using heat and pressure. It is of great importance in industries such as construction, manufacturing, automotive, and aerospace. The ability to create strong and durable bonds between metal components is essential for the successful operation of various industries.
Different Types Of Welding Techniques
The quickest welding type is MIG (Gas Metal Arc Welding – GMAW). It is highly productive, easy to learn, and can be used on flux-cored welding projects. Stick welding, on the other hand, is slower and less efficient.
Read More: What is The Most Important Thing in Welding?
There are various welding techniques available, each suited for different applications. Whether you need a quick and efficient method or a precise and clean weld, understanding the different types of welding techniques can help you choose the right one for your project.
Here is an overview of the most common welding techniques:
- Stick Welding (Shielded Metal Arc Welding – SMAW):
- This technique uses an electrode coated in flux to create an arc and join the metals together.
- It is a versatile method that can be used on thick metals and in outdoor conditions.
- Stick welding is commonly used in construction, fabrication, and maintenance projects.
- Flux Core Arc Welding – FCAW:
- FCAW is similar to stick welding, but it uses a continuously fed electrode with flux inside.
- It is a high-speed technique and suitable for welding thick materials.
- FCAW is often used in shipbuilding, construction, and the automotive industry.
- MIG Welding (Gas Metal Arc Welding – GMAW):
- MIG welding uses a wire electrode and an inert gas to protect the weld from atmospheric contamination.
- It is a fast and relatively easy technique suitable for welding thin and thick materials.
- MIG welding is widely used in manufacturing, automotive, and fabrication industries.
- TIG Welding (Gas Tungsten Arc Welding – GTAW):
- TIG welding uses a non-consumable tungsten electrode and an inert gas for shielding.
- It produces precise, high-quality welds and is commonly used for thin materials and non-ferrous metals.
- TIG welding is popular in aerospace, automotive, and artistic applications.
- Gas tungsten arc welding:
- This technique uses a tungsten electrode and a shielding gas to weld non-ferrous metals.
- It provides excellent control over the weld and is suitable for precise and high-quality welds.
- Gas tungsten arc welding is commonly used in aircraft manufacturing, bike frames, and jewelry making.
- Flux-cored arc welding:
- Similar to MIG welding, flux-cored arc welding uses a continuously fed electrode with flux inside.
- It is ideal for welding thick materials and is commonly used in construction, shipbuilding, and heavy equipment fabrication.
- Oxy-fuel welding and cutting:
- Oxy-fuel welding combines oxygen and fuel gases to create a high-temperature flame for welding and cutting.
- It is primarily used for welding thin materials, heating, and metal cutting operations.
- Oxy-fuel welding is often utilized in repairs, plumbing, and metal sculpture.
- Electric resistance welding:
- Electric resistance welding uses the heat generated by electrical resistance to join metals.
- It is a fast and efficient method that requires no filler material.
- Electric resistance welding is commonly used in the automotive industry for spot welding.
- Atomic hydrogen welding:
- Atomic hydrogen welding uses hydrogen gas to produce a high-temperature flame for welding.
- It is a precise technique suitable for welding non-ferrous metals and stainless steel.
- Atomic hydrogen welding is often used in the aerospace industry.
- Electroslag welding:
- Electroslag welding is a method that uses an electric current passed through a flux and metal to create the weld.
- It is used for welding large and thick materials and is popular in shipbuilding and bridge construction.
Understanding the different welding techniques allows you to choose the fastest and most appropriate method for your project. Whether you need speed, precision, or versatility, there is a welding technique that can meet your requirements.
Gas Metal Arc Welding (Gmaw)
Gas Metal Arc Welding (GMAW), also known as MIG welding, is considered one of the quickest welding types. It is easy to learn and operate, making it suitable for beginners while maintaining high productivity levels.
Introduction To Gmaw And Its Key Features
, also known as MIG (Metal Inert Gas) Welding, is a versatile and popular welding technique used in various industries. It involves creating an arc between a continuous wire electrode and the workpiece while shielding the weld area with an inert gas.
Here are some key features of GMAW:
- Gas Metal Arc Welding is a semi-automatic process that offers high welding speed and efficiency.
- It is relatively easy to learn and suitable for both beginners and experienced welders.
- GMAW can be used to join a wide range of materials such as carbon steel, stainless steel, aluminum, and more.
- The use of a shielding gas protects the weld from atmospheric contamination, resulting in clean and strong welds.
- This welding process allows for precise control over the arc, wire feed speed, and voltage, ensuring consistent and high-quality welds.
Advantages And Disadvantages Of Gmaw
GMAW offers several advantages that make it a preferred choice for many welding applications. Here are some of the benefits:
- High welding speed: GMAW allows for fast deposition rates, making it an efficient welding technique, especially for large-scale projects.
- Versatility: This welding process can be used on a wide range of materials, including thin sheets and thick plates.
- Good weld appearance: GMAW produces clean and aesthetically pleasing welds with minimal spatter, reducing cleanup time.
- Less post-weld cleaning: The use of a shielding gas helps prevent the formation of slag or flux, eliminating the need for post-weld cleaning.
- Easy automation: GMAW can be easily automated with welding robots, increasing productivity and reducing labor costs.
However, GMAW also has its limitations and disadvantages:
- Limited outdoor application: GMAW requires a shielding gas, which can be challenging to use in outdoor environments with windy conditions.
- Dependence on consumables: The use of filler wire and shielding gas adds to the overall cost of GMAW.
- Alloy limitations: GMAW may not be suitable for welding certain high-alloy steels or dissimilar metals.
Applications And Industries Where GMAW is Commonly Used
Gas Metal Arc Welding is widely used in various industries due to its versatility and speed. Here are some common applications:
- Automotive: GMAW is commonly used in the automotive industry for welding car frames, exhaust systems, and various components.
- Construction: It is used for welding structural steel, pipelines, and other metal structures in the construction industry.
- Fabrication: GMAW is extensively used in metal fabrication shops for welding gates, fences, handrails, and other custom metal products.
- Manufacturing: This welding process is utilized in the manufacturing of appliances, furniture, machinery, and other metal-based products.
- Aerospace: GMAW is used in the aerospace industry for welding aircraft components, such as fuselages, wings, and engine parts.
Gas Metal Arc Welding offers speed, versatility, and high-quality welds, making it a go-to choice for many welding applications in various industries.
Shielded Metal Arc Welding (Smaw)
Shielded Metal Arc Welding (SMAW) is not the quickest welding type. MIG welding is known for its high productivity and ease of learning, making it a faster and more efficient option. TIG welding, on the other hand, is slower but allows for finer and more precise welds.
Shielded Metal Arc Welding (SMAW), also known as stick welding, is a popular welding technique that offers both advantages and disadvantages. This section will delve into the key features of SMAW, its advantages and disadvantages, as well as the industries and applications where it is commonly used.
Introduction To Smaw And Its Key Features
- SMAW is a welding process that uses a flux-coated electrode to create an electric arc between the electrode and the base metal. The heat generated from the arc melts the electrode and the base metal, fusing them to form a weld.
- Key features of SMAW include its simplicity, versatility, and portability. It can be used in various positions, including flat, vertical, overhead, and horizontal, making it suitable for a wide range of welding applications.
Advantages And Disadvantages Of Smaw
Advantages of SMAW:
- Suitable for outdoor and remote locations: SMAW can be performed in outdoor and remote locations as it does not require a shielding gas like other welding techniques. This makes it a preferred choice in construction sites and areas without access to electricity.
- Versatility: SMAW can be used on various materials, including carbon steel, stainless steel, cast iron, and non-ferrous metals.
- Easy setup and equipment requirements: SMAW equipment is relatively simple and requires minimal setup compared to other welding techniques. This makes it more accessible for beginners and those with limited resources.
Disadvantages of SMAW:
- Lower productivity: SMAW has a lower deposition rate compared to other welding techniques such as MIG or TIG welding. This means that it may take longer to complete a welding project using SMAW.
- Slag and spatter: SMAW produces slag and spatter during the welding process, which requires additional cleaning and finishing work to achieve a smooth and clean weld.
- Limited joint access: SMAW can be challenging to use in tight and confined spaces due to the size and shape of the electrodes. This makes it less suitable for applications that require precise and intricate welds.
Applications And Industries Where Smaw Is Commonly Used
SMAW is commonly used in a variety of industries and applications, including:
- Construction: SMAW is widely used in the construction industry for welding structural steel, pipelines, and heavy machinery.
- Maintenance and repair: SMAW is often utilized in maintenance and repair work, such as fixing equipment, repairing vehicles, and joining metal components.
- Shipbuilding: SMAW is commonly used in shipbuilding due to its versatility, portability, and ability to weld thick steel plates.
- Infrastructure: SMAW is employed in the construction and repair of infrastructure, including bridges, buildings, and highways.
- Offshore and remote locations: SMAW is preferred in offshore and remote locations, where access to electricity and shielding gases may be limited.
SMAW, or shielded metal arc welding, is a versatile welding technique that offers simplicity, portability, and suitability for outdoor and remote locations. While it has advantages such as its versatility and ease of setup, it also has disadvantages, including lower productivity and the need for additional cleaning work.
Despite its limitations, SMAW is widely used in the construction, maintenance and repair, shipbuilding, and infrastructure industries.
Flux Core Arc Welding (Fcaw)
Flux Core Arc Welding (FCAW) is considered one of the quickest welding types. It allows for high productivity and is easy to learn, making it a popular choice even for beginners.
Explanation Of Fcaw And Its Key Features:
- Is a type of welding process that uses a continuously-fed tubular electrode filled with flux to create the weld joint.
- FCAW is similar to MIG welding, but it does not require a shielding gas because the flux inside the electrode produces a protective shield around the weld pool.
- This welding method is known for its high welding speed and deposition rate, making it one of the quickest welding types available.
- FCAW can be used in both indoor and outdoor environments, making it versatile and convenient for various applications.
Gas Tungsten Arc Welding (Gtaw)
Gas Tungsten Arc Welding (GTAW), also known as TIG welding, is the quickest welding type for creating consistent and fine welds. It offers deeper penetration and is efficient for a wide range of projects.
Introduction To Gtaw And Its Key Features:
, also known as Tungsten Inert Gas (TIG) welding, is a welding process that uses a tungsten electrode to produce the weld. This type of welding is often considered one of the most precise and cleanest welding methods available. Here are the key features of GTAW:
- GTAW involves the use of a non-consumable tungsten electrode that creates an arc to heat and melt the base metals. This electrode is protected by an inert gas such as argon, which prevents oxidation and contamination of the weld area.
- The heat generated by the arc melts the base metals, and a filler rod is added to create the weld joint. This process allows for precise control of the weld pool and minimizes the risk of defects, such as porosity and spatter.
- GTAW can be used to weld a wide range of materials, including stainless steel, aluminum, copper, and titanium. It is particularly suitable for thin gauge materials, as it produces high-quality, cosmetically appealing welds with minimal deformations.
- The process allows for better control over the heat input, which reduces the risk of distortion and warping in the welded parts. This makes GTAW ideal for applications that require tight tolerances and aesthetic appeal.
- GTAW produces welds with exceptional strength and structural integrity. The process allows for full penetration welds, resulting in joints that are highly resistant to cracking and fatigue.
- One of the unique features of GTAW is its ability to perform precise welds in challenging positions, including overhead and vertical positions. This versatility makes GTAW a preferred choice for welding pipes, tubes, and other complex structures.
Advantages And Disadvantages Of Gtaw:
GTAW offers several advantages and disadvantages that should be considered when choosing a welding method. Here are the key points:
Advantages:
- GTAW produces high-quality welds with excellent aesthetics, making it suitable for applications that require a visually appealing finish.
- The process allows for precise control over the weld pool, resulting in minimal distortion and shrinkage.
- GTAW can be used to weld a wide range of materials, including those with high heat sensitivity, such as stainless steel and aluminum.
- The use of inert gas as a shielding medium ensures a clean and contamination-free weld, resulting in strong and durable joints.
- GTAW is versatile and can be used in various positions, making it suitable for welding complex shapes and structures.
Disadvantages:
- GTAW is a slower welding process compared to other methods, such as MIG welding. It requires greater skill and patience, which can increase the overall welding time.
- The equipment for GTAW is more expensive compared to other welding processes, making it less economical for large-scale projects.
- The process is less suited for thick materials, as it may require multiple passes to achieve full penetration.
Applications And Industries Where Gtaw Is Commonly Used:
GTAW finds its application in various industries and is preferred for specific applications. Some common uses of GTAW include:
- Aerospace industry: GTAW is widely used in the aerospace industry for welding critical components, such as aircraft frames, engine components, and fuel tanks. The process’s ability to produce high-quality, defect-free welds makes it ideal for ensuring the structural integrity and safety of aerospace structures.
- Medical industry: GTAW is commonly used in the medical industry for welding stainless steel and titanium components, such as surgical instruments, implants, and medical devices. The process’s cleanliness and precision make it suitable for applications that require biocompatibility and corrosion resistance.
- Food and beverage industry: GTAW is often employed for welding stainless steel components used in the food and beverage industry, such as tanks, pipelines, and processing equipment. The process ensures sanitary welds and prevents contamination of the products.
- Automotive industry: GTAW is used in the automotive industry for welding components that require high strength, such as exhaust systems, suspension parts, and engine components. The process’s ability to produce high-quality welds with excellent fatigue resistance makes it suitable for automotive applications.
- Artistic and fabrication industry: GTAW is popular in the artistic and fabrication industry for its ability to create intricate designs and welds with superior aesthetics. It is used for welding sculptures, decorative pieces, and architectural structures.
GTAW, also known as TIG welding, is a precise and clean welding process that offers several advantages in terms of weld quality and control. While it may be slower and more expensive compared to other welding methods, GTAW finds applications in various industries where aesthetics, strength, and precision are crucial.
Its ability to produce high-quality welds on a wide range of materials makes GTAW a versatile and preferred choice for many welding applications.
Comparison Of Welding Techniques
Looking for the quickest welding type? MIG welding is known for its high productivity and ease of learning, making it a fast and efficient option for beginners. Stick welding, on the other hand, may be slower and less efficient in comparison.
Read More: What Position is Hardest in Welding?
Productivity and efficiency. However, it’s important to consider various factors when choosing the quickest welding type. Let’s dive into a detailed comparison of the welding techniques discussed above.
A Detailed Comparison Of The Welding Techniques Discussed Above:
- Stick Welding (Shielded Metal Arc Welding – SMAW):
- Involves using a stick electrode to create an arc between the electrode and the metal being welded.
- Ideal for outdoor applications and working on thick metal.
- Flux Core Arc Welding – FCAW:
- Similar to MIG welding but utilizes a flux-cored electrode that creates gas and slag during the welding process.
- Provides better penetration and is suitable for working on thicker metals.
- MIG Welding (Gas Metal Arc Welding – GMAW):
- Uses a wire electrode that is fed through a welding gun, while a shielding gas protects the weld from atmospheric contamination.
- Fast and efficient, making it the go-to choice for various applications.
- TIG Welding (Gas Tungsten Arc Welding – GTAW):
- Utilizes a non-consumable tungsten electrode and a shielding gas to create a precise and clean weld.
- Offers excellent control and produces high-quality welds, but may take longer than other techniques.
When choosing the quickest welding type, it’s essential to consider the following factors:
- Material thickness: Thicker materials may require techniques like stick welding or flux core welding for better penetration.
- Conditions and environment: Outdoor or windy conditions may favor stick welding, while controlled environments may allow for other techniques.
- Skill level and experience: Each welding technique has its own learning curve, so consider your skill level and experience when making a choice.
- Project requirements: The specific requirements of your project, such as welding position, aesthetics, and welding length, may influence the welding technique you choose.
By weighing these factors and considering the pros and cons of each technique, you can determine the quickest welding type that best suits your needs. Remember to prioritize efficiency, productivity, and the quality of the final weld.
Factors Affecting Welding Speed
The quickest welding type is MIG welding, which is highly productive and easy to learn even for beginners. MIG welding uses a feed wire that runs through the machine at a preselected speed, resulting in fast and consistent welds.
Various Factors That Impact The Speed Of Different Welding Techniques:
- Power source: The type and power of the welding machine can significantly affect the welding speed. Higher-power machines often provide faster and more efficient welding.
- Skill and experience: The welding technique requires expertise and experience. Skilled welders can complete the process faster compared to beginners.
- Joint design: The complexity and design of the joint being welded can affect the speed. Simple joints with easy access are typically faster to weld.
- Welding position: Different welding positions, such as flat, horizontal, vertical, or overhead, can impact welding speed. Some positions may require more time and effort to achieve a proper weld.
- Welding material: The type and thickness of the material being welded can influence the speed. Some materials may require slower welding speed to avoid defects or ensure proper fusion.
- Welding technique: Each welding technique, such as MIG, TIG, or stick welding, has its own speed capabilities. Some techniques are inherently faster than others.
Tips For Optimizing Welding Speed And Efficiency:
- Prepare the work area: Ensure the work area is clean, free from debris, and properly set up for welding. This minimizes interruptions and helps maintain a smooth workflow.
- Use the right equipment: Select the appropriate welding machine, electrode, filler wire, or shielding gas for the specific welding job. The right equipment can make the process faster and more efficient.
- Maintain consistent arc length: Keep the arc length consistent throughout the weld to ensure proper fusion and reduce the need for rework or corrections.
- Weld in a continuous motion: Maintain a steady and continuous motion while welding to achieve a uniform bead appearance and reduce the time spent on each joint.
- Optimize travel speed: Finding the right balance between travel speed and heat input is crucial. Experiment with different travel speeds to determine the optimal speed for the specific material and joint.
- Minimize unnecessary stops and starts: Avoid unnecessary stops and starts during the welding process. Continuity helps maintain the welding arc and reduces the time spent on restarting and reestablishing the arc.
- Consider automation: For large-scale projects, consider using automated welding systems to optimize speed and efficiency.
- Continuously improve skills: Regularly update and improve welding skills through training and practice. Skilled welders can complete the process faster and more efficiently.
Remember, the welding speed can vary depending on various factors, and it is essential to find the right balance between speed and quality to ensure a successful weld.
Fastest Welding Technique
MIG welding is considered the fastest welding technique, leading to high productivity and easy learning for beginners. It utilizes a feed wire that runs through the machine, making the process relatively fast and producing consistent welds.
Gh productivity and efficiency. It is commonly used in the automotive, construction, and manufacturing industries. Here are the factors to consider when determining the fastest welding technique:
- Speed: MIG welding, also known as Gas Metal Arc Welding (GMAW), is known for its high welding speed. It uses a continuously fed electrode wire, which allows for faster and continuous welding.
- Automation: MIG welding can be easily automated using robotic systems, increasing production speed and reducing human error. This makes it ideal for large-scale production lines.
- Ease of use: MIG welding is relatively easy to learn and operate compared to other welding techniques. This means less time spent on training and more time spent on actual welding.
- Versatility: MIG welding can be used on a wide range of materials, including steel, stainless steel, aluminum, and copper. This versatility makes it a preferred choice for various applications.
- Cost-effective: MIG welding equipment is generally more affordable compared to other welding machines. Additionally, the use of wire electrodes instead of expensive filler rods further reduces the overall cost of welding.
- Strong and durable welds: MIG welding produces strong and durable welds that have good structural integrity. This is important for applications where weld strength is crucial, such as in structural fabrication.
- Reduced post-weld cleaning: MIG welding produces clean welds with minimal spatter, reducing the need for extensive post-weld cleaning and finishing.
- High deposition rate: MIG welding can achieve a high deposition rate, which means more metal can be deposited in a shorter amount of time. This is especially beneficial for applications that require rapid welding.
MIG welding is widely considered the fastest welding technique due to its high speed, automation capabilities, ease of use, versatility, cost-effectiveness, strong welds, reduced post-weld cleaning, and high deposition rate. Whether you are working on a small project or a large-scale production line, MIG welding can provide you with efficient and effective results.
Choosing The Right Welding Technique
Looking for the quickest welding type? MIG welding is known for its high productivity and ease of learning, making it a fast and efficient choice. Stick welding, on the other hand, may require more time and effort to set up and master.
Techniques available. It utilizes a continuously fed wire electrode, which allows for a high welding speed and efficient deposition of filler material. The arc is shielded by a protective gas, typically argon or a mixture of argon and carbon dioxide, which prevents the weld pool from contamination and oxidation.
Factors To Consider When Selecting A Welding Technique For A Specific Project:
- Material type and thickness: Different welding techniques are better suited for specific materials and thicknesses. Consider the compatibility of the welding technique with the material you are working with.
- Joint design: The type of joint, whether it is a butt joint, lap joint, or fillet joint, will determine the best welding technique to use. Some techniques are better suited for certain joint designs.
- Weld quality requirements: Consider the required strength, appearance, and structural integrity of the weld. Certain techniques may produce higher-quality welds than others.
- Accessibility: Consider the accessibility of the welding area. Some techniques are more easily maneuverable in tight spaces, while others may require more room.
- Project timeline and cost: The welding technique you choose may impact the overall project timeline and cost. Consider the speed and efficiency of the technique and whether it aligns with your project requirements and budget.
Tips For Making An Informed Decision Based On Project Requirements:
- Consult with a welding expert or engineer: Seek professional advice to determine the most suitable welding technique for your specific project requirements.
- Conduct material testing: Perform tests on your material to determine its weldability and which techniques are best suited for it.
- Evaluate cost-effectiveness: Consider the cost of different welding techniques, including equipment, consumables, and labor, about your project budget.
- Prioritize safety: Ensure that the chosen welding technique aligns with safety requirements and that your team is trained and equipped to handle it properly.
- Consider future maintenance and repair: Anticipate whether the chosen welding technique will allow for ease of maintenance and repair, should it be required in the future.
By carefully considering these factors and following these tips, you can make an informed decision when selecting the right welding technique for your specific project. Remember to prioritize factors such as material compatibility, joint design, weld quality, accessibility, project timeline, and cost-effectiveness to ensure a successful welding outcome.
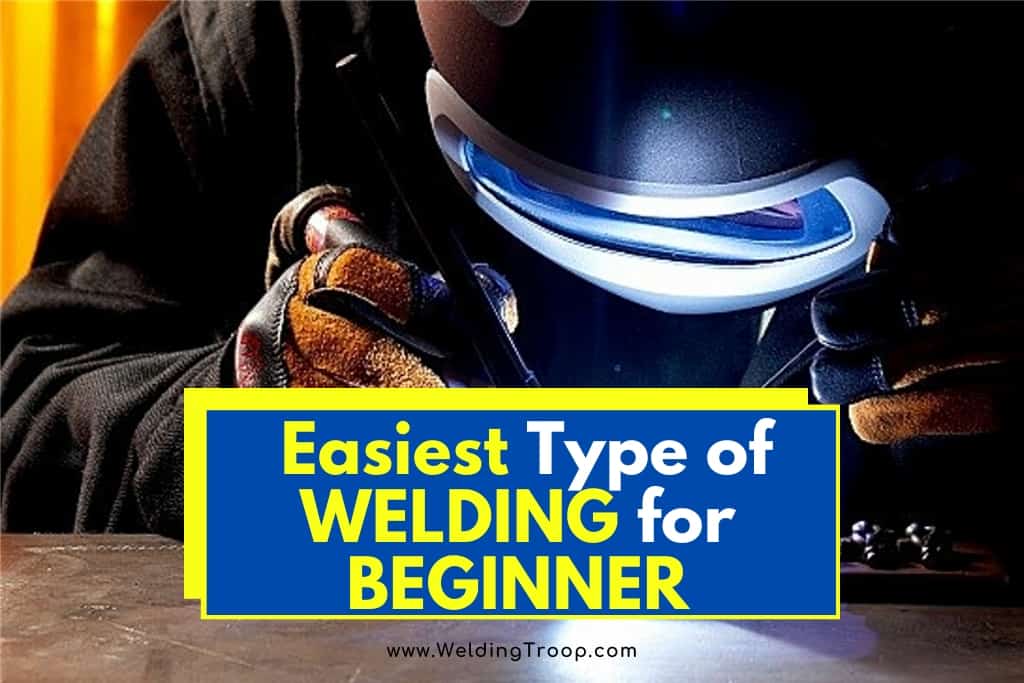
Credit: weldingtroop.com
Frequently Asked Questions On What Is The Quickest Welding Type?
What Type Of Welding Is The Fastest?
The fastest type of welding is MIG welding, which leads to high productivity and is easy to learn and operate.
What’s The Easiest Welding Type?
MIG welding is generally the easiest type of welding to learn. It’s fast, produces consistent welds, and uses a feed wire for efficient operation.
Is Tig Welding Slower Than Mig?
The TIG welding process is slower than MIG welding due to the narrower arc and the need to hand-feed the filler wire.
Is Mig Welding Faster Than Stick Welding?
MIG welding is faster and more efficient than stick welding. It is also cleaner and easier to learn, although the setup and cost may be higher.
What Is The Fastest Welding Method?
MIG welding is one of the fastest welding methods, leading to high productivity and an easier learning curve.
Conclusion
Ering the techniques, making it a suitable choice for beginners. Additionally, MIG welding offers high productivity due to its fast speed, making it a popular choice in manufacturing industries. Another advantage of MIG welding is its ability to be used on flux-cored welding projects, offering versatility in application.
On the other hand, TIG welding provides finer welds and deeper penetrations, although it is generally slower due to the need for hand-feeding the filler wire. While TIG welding may require more skill and experience, it can produce high-quality results.
Ultimately, the choice between MIG and TIG welding depends on the specific requirements of the project and the skill level of the welder. Whether you need speed or precision, both welding types have their own advantages to offer. So, consider the factors and choose the welding type that best suits your needs.
Happy welding!