The most important thing in welding is safety. Without proper safety measures, welding can pose serious risks to both the welder and the environment.
Welders must prioritize wearing protective gear, such as goggles, gloves, and welding helmets, to protect themselves from burns, sparks, and harmful fumes. Additionally, ensuring a well-ventilated workspace and using fire-resistant materials are essential for preventing accidents and fires. By prioritizing safety, welders can maintain a secure and healthy work environment.
In the field of welding, safety is of utmost importance. Welding involves the process of joining metal components together by melting and fusing them using heat or pressure. While it is a crucial technique used in various industries, such as construction, automotive, and manufacturing, it also presents potential hazards that should not be taken lightly.
Therefore, the most important aspect of welding is to prioritize safety to minimize the risk of accidents, injuries, and long-term health issues. This requires welders to adhere to strict safety protocols, wear appropriate protective gear, and maintain a safe working environment. By emphasizing safety, welders can ensure the well-being of themselves, their peers, and the overall success of their welding projects.
Understanding The Importance Of Welding Techniques
Understanding the importance of welding techniques is crucial in achieving high-quality welds. The most important thing in welding is to have proper training and certification, as well as the ability to handle different welding processes and materials. Welders work in challenging environments and must have the focus and skill to execute their craft flawlessly.
Welding techniques play a vital role in ensuring the quality and durability of welds. Employing the right welding techniques can make a significant difference in the outcome of a welding project. Whether you are a professional welder or a DIY enthusiast, understanding the importance of welding techniques is crucial for successful welds.
In this section, we will explore the role of welding in various industries, the benefits of proper welding techniques, and common welding mistakes to avoid.
The Role Of Welding In Various Industries:
- Construction Industry:
- Welding is essential in the construction industry for joining structural members and fabricating large-scale metal structures such as buildings, bridges, and skyscrapers.
- Proper welding techniques ensure the structural integrity and safety of these constructions.
- Automotive Industry:
- In the automotive industry, welding is used for manufacturing vehicle frames, exhaust systems, and various components.
- Precise welding techniques help in creating strong and durable connections, ensuring vehicle safety and performance.
- Aerospace Industry:
- Welding plays a critical role in the aerospace industry, where the highest standards of quality and precision are required.
- Welded connections are used in aircraft structures, engines, and other components, and adherence to specific welding procedures is crucial for maintaining flight safety.
- Energy Sector:
- The energy sector, including oil and gas, relies on welding for constructing pipelines, storage tanks, and refineries.
- Welding techniques, such as pipeline welding, ensure leak-free joints and the integrity of these crucial energy infrastructures.
Benefits Of Proper Welding Techniques:
- Strength and Durability:
- Employing proper welding techniques enhances the strength and durability of the welded joints, ensuring longevity and reliability.
- Aesthetic Appeal:
- The use of appropriate welding techniques results in visually appealing welds, contributing to the overall aesthetics of the finished product.
- Efficiency and Cost-Effectiveness:
- Proper welding techniques optimize the welding process, reducing rework and minimizing material waste, leading to increased efficiency and cost savings.
- Enhanced Safety:
- By following proper welding techniques, welders can mitigate the risk of weld failures, ultimately ensuring the safety of the structures or equipment being welded.
Common Welding Mistakes To Avoid:
- Insufficient Joint Preparation:
- Inadequate cleaning and preparation of the joint surfaces can lead to weak welds and potential failures.
- Incorrect Welding Parameters:
- Failure to use the correct welding settings, such as voltage, amperage, and wire speed, can result in poor weld quality and decreased strength.
- Inadequate Heat Control:
- Improper heat control, either too much or too little, can cause distortion, cracking, or ineffective fusion of the base metals.
- Lack of Welder Skill and Experience:
- Insufficient training and experience can lead to subpar welds, as proper technique execution requires knowledge and practice.
- Poor Welding Positioning and Technique:
- Welding in uncomfortable positions or using improper welding techniques can result in inconsistent welds and compromise the overall quality.
Understanding the importance of welding techniques is essential for achieving successful and reliable welds. By recognizing the role welding plays in various industries, appreciating the benefits of proper techniques, and knowing the common mistakes to avoid, you can enhance your welding skills and ensure superior weld quality.
Choosing The Right Welding Equipment
Choosing the right welding equipment is crucial in ensuring successful welding projects. The most important thing in welding is selecting equipment that suits your specific welding needs, taking into consideration factors such as the type of welding process and materials being used.
Read More: What Position is Hardest in Welding?
When it comes to welding, one of the most crucial aspects is choosing the right welding equipment. Whether you are a professional welder or a hobbyist, having the appropriate tools and machinery is essential for achieving quality welds and ensuring safety.
Here are some key considerations to keep in mind when selecting welding equipment:
Key Considerations When Selecting Welding Equipment:
- Budget: Determine your budget and look for welding equipment that offers the best value for your money.
- Welding Process: Different welding processes require specific types of equipment. Consider whether you need a MIG welder, TIG welder, Stick welder, or any other specialized machine.
- Power Source: Decide whether you need a machine that runs on electricity, gas, or both, depending on your welding requirements.
- Portability: If you need to move your welding equipment frequently or work on different job sites, consider the weight and portability of the machine.
- Duty Cycle: The duty cycle determines how long you can weld continuously before the machine needs to cool down. Calculate your projected welding time and choose equipment with an adequate duty cycle.
Understanding Different Types Of Welding Machines:
There are various types of welding machines available, each designed for different welding processes. It’s crucial to understand the differences and select the right machine for your specific needs. Here are some common types of welding machines:
- MIG Welders: MIG (Metal Inert Gas) welders are versatile and widely used for welding different metals. They are known for their ease of use and fast welding speed.
- TIG Welders: TIG (Tungsten Inert Gas) welders are often preferred for precise and high-quality welds. They are commonly used in industries that require exceptional welding precision.
- Stick Welders: Stick welders, also known as arc welders, are suitable for heavy-duty welding tasks and outdoor use. They work well with thicker metals and provide strong welds.
- Plasma Cutters: Plasma cutters are primarily used for cutting metal, but they can also be used for welding. They offer clean and precise cuts in various metal thicknesses.
- Multi-Process Welders: Multi-process welders are versatile machines that can perform multiple welding processes, making them suitable for various applications.
Importance Of Quality Welding Tools And Accessories:
Having high-quality welding tools and accessories is vital for achieving accurate and reliable welds. Here’s why investing in quality equipment is crucial:
- Safety: Poor-quality welding tools may compromise safety, leading to accidents or faulty welds. High-quality equipment is designed with safety features to protect the welder and prevent hazardous situations.
- Durability and Performance: Quality tools and accessories are built to last, ensuring long-term reliability and consistent performance. They can withstand the demanding conditions of welding and provide optimal results.
- Efficiency: With quality tools, you can work more efficiently, saving time and effort. They offer better control, precision, and ease of use, enabling you to produce high-quality welds with less effort.
- Consistency and Quality: Using top-notch tools and accessories contributes to consistent and high-quality welds. They help to achieve precise welds with minimal defects, ensuring the integrity and strength of the finished product.
Choosing the right welding equipment plays a vital role in achieving successful welds and ensuring safety. Consider the key considerations when selecting equipment, understand the different types of machines available, and prioritize investing in quality tools and accessories for optimal results.
Safety Measures In Welding
To ensure safety in welding, the most important aspect is to prioritize the prevention of electric shock. Welders must be educated and trained to minimize the risk of this hazard, which can have immediate and severe consequences.
Welding is a crucial process in various industries, but it can also pose certain risks to the welders if proper safety measures are not taken. To ensure the well-being of the workers and maintain a safe working environment, it is crucial to implement the following safety measures:
Essential Safety Equipment For Welders
- Welding Helmet: A welding helmet is a must-have for welders to protect their face, eyes, and neck from harmful ultraviolet (UV) and infrared (IR) rays emitted during the welding process.
- Welding Gloves: Welding gloves provide hand and arm protection from sparks, heat, and electric shock. They are usually made of flame-resistant leather or other durable materials.
- Safety Glasses or Goggles: Apart from the welding helmet, welders should also wear safety glasses or goggles to safeguard their eyes from flying debris and particles.
- Fire-Resistant Clothing: Welders should wear fire-resistant clothing, such as a long-sleeved shirt, pants, and closed-toe shoes, to minimize the risk of burns caused by sparks and flames.
- Respiratory Protection: Welding fumes can be hazardous, so welders need to wear respiratory protection, such as a respirator or dust mask, to protect their lungs from inhaling harmful particulates.
Importance Of Proper Ventilation And Fume Extraction
- Adequate Ventilation: Proper ventilation is crucial in welding areas to ensure the removal of welding fumes and gases. Good ventilation helps maintain air quality and reduces the risk of respiratory issues.
- Fume Extraction Systems: Fume extraction systems, such as local exhaust ventilation (LEV) systems or portable fume extractors, should be used to capture and remove welding fumes at the source. This helps protect both the welder and others in the vicinity from the harmful effects of fume inhalation.
Handling Welding Hazards And Preventing Accidents
- Training and Education: Proper training should be provided to welders to ensure they are aware of the hazards associated with the welding process and understand the necessary safety precautions. This education should cover topics like fire prevention, electrical safety, and proper handling of welding equipment.
- Housekeeping: Maintaining a clean and organized work environment is crucial for preventing accidents. Removing tripping hazards, keeping welding cables and hoses out of the way, and ensuring proper storage of flammable materials can significantly reduce the risk of accidents.
- Equipment Maintenance: Regular inspection and maintenance of welding equipment is essential to ensure its proper functioning and minimize the risk of malfunctions or accidents.
- Fire Safety: Welding involves the use of high heat, sparks, and flammable materials, making fire safety protocols critical. Fire extinguishers should be readily available, and workers should be trained in their proper use.
By implementing these safety measures, the risk of accidents, injuries, and long-term health hazards associated with welding can be significantly reduced. Prioritizing safety not only protects the welders but also fosters a productive and secure work environment.
Material Selection For Welding
The most important thing in welding is material selection. Choosing the right material for welding is crucial as it affects the quality and strength of the weld. Consider factors such as the type of metal, its composition, and its properties to ensure a successful weld.
Importance Of Choosing The Right Welding Materials:
Selecting the appropriate materials for welding is crucial for achieving strong and durable welds. The right choice of welding materials ensures optimal performance and longevity of the welded structure. Here are some key reasons why material selection is of utmost importance in welding:
- Strength and Durability: Different metals have varying tensile strengths and resistances to stress and corrosion. Choosing the right welding materials ensures that the welded structure retains its strength and durability over time.
- Compatibility: Welding materials should be compatible with the base metals to ensure a strong weld joint. Using mismatched materials can result in weak welds, leading to failure or deformation of the welded structure.
- Heat Affected Zone (HAZ): The HAZ refers to the region near the weld where the base metal experiences changes in its mechanical and metallurgical properties. Proper material selection helps minimize the negative effects of heat on the HAZ, reducing the risk of cracks, distortion, or other welding defects.
- Cost Efficiency: Selecting the right welding materials can help optimize the cost of the welding process. Some materials may be more expensive, but they offer superior performance and longevity, reducing the need for frequent repairs or replacements.
To ensure successful welding, it is essential to consider various factors when selecting welding metals.
Welding Process Optimization
The most important thing in welding is safety, with a particular focus on preventing electric shocks. Welders should be well-educated on the risks and take necessary precautions to ensure their safety while working.
Importance Of Efficient Welding Processes:
Efficient welding processes play a crucial role in the welding industry. It not only helps save time and money but also ensures the production of high-quality welds. Here are some key points highlighting the importance of efficient welding processes:
- Enhances Productivity: Efficient welding processes increase productivity by reducing the time required for each weld. This allows companies to complete projects more quickly and meet deadlines.
- Improves Weld Quality: A well-optimized welding process ensures consistent and reliable weld quality. It minimizes the chances of defects such as cracks, porosity, and lack of fusion, resulting in stronger and more durable welds.
- Reduces Costs: By increasing productivity and minimizing rework, efficient welding processes help reduce costs associated with labor, materials, and equipment. It also decreases downtime and increases overall profitability.
- Ensures Safety: Optimal welding processes contribute to a safer working environment. It minimizes the risks of accidents, such as burns or exposure to harmful fumes, by implementing proper safety measures and suitable welding techniques.
- Adaptable to Various Materials: Efficient welding processes can be tailored to work with various materials, including different types of metal alloys and thicknesses. This versatility allows welders to handle a wide range of projects and materials.
Key Factors For :
To achieve efficient welding processes, several key factors need to be considered. These factors contribute to the optimization of the welding process and ensure the best possible results. Here are the key factors for welding process optimization:
- Welding Parameters: Properly setting welding parameters, such as voltage, current, and travel speed, is essential for achieving the desired weld quality. Optimizing these parameters based on the specific welding application helps ensure consistent and optimal results.
- Material Preparation: Before starting the welding process, proper material preparation is vital. It includes cleaning the base metal to remove any contaminants, ensuring precise fit-up, and selecting the appropriate filler metal for the application.
- Welding Technique Selection: Different welding techniques, such as MIG (Metal Inert Gas), TIG (Tungsten Inert Gas), or Stick welding, have their advantages and limitations. Selecting the most suitable technique for the specific project helps optimize the welding process.
- Welding Equipment and Consumables: Using high-quality welding equipment and consumables, such as welding machines, electrodes, and shielding gases, significantly impacts the welding process’s efficiency and the final weld quality.
- Training and Skill Development: Continuous training and skill development are crucial for welders to effectively optimize the welding process. Keeping up with the latest advancements in welding techniques and technologies helps improve efficiency and quality.
Improving Productivity And Quality Through Process Optimization:
Process optimization is not only beneficial for efficiency but also plays a vital role in enhancing productivity and weld quality. Here are some ways process optimization improves productivity and quality:
- Reducing Non-Value-Added Time: By eliminating unnecessary steps or reducing setup time, process optimization allows welders to spend more time on actual welding, leading to increased productivity.
- Minimizing Rework and Defects: Through proper process optimization, the occurrence of weld defects can be minimized. This reduces the need for rework, saving time, and improving overall productivity.
- Ensuring Consistency: Following optimized welding processes ensures consistent results across different welds, leading to better quality control and higher customer satisfaction.
- Optimizing Weld Cycle Time: Efficient process optimization helps speed up the welding cycle while maintaining quality standards. This leads to improved productivity without compromising weld quality.
- Continuous Improvement: Process optimization should be an ongoing effort, with regular evaluation and adjustment of parameters and techniques. By continually improving the welding process, productivity and quality can be consistently enhanced.
Efficient welding processes, achieved through optimization, are crucial for enhancing productivity, reducing costs, and ensuring high-quality welds. By considering key factors and continually striving for process improvement, welders and fabrication companies can achieve optimal results in their welding projects.
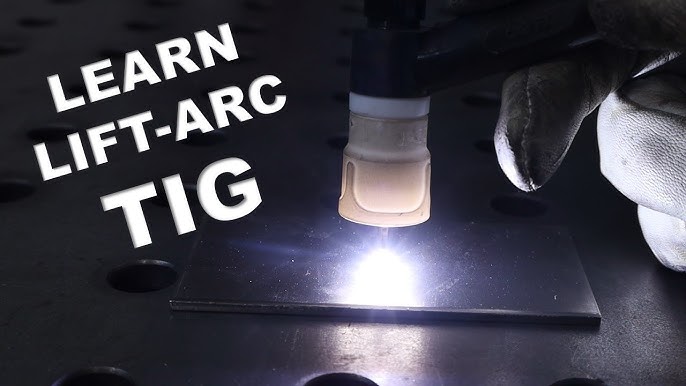
Credit: www.youtube.com
Welding Inspection And Quality Control
Welding inspection and quality control are crucial aspects of the welding process. The most important thing in welding is ensuring that the welds meet the required standards for strength and durability. Proper inspection and quality control measures guarantee that the welds are free from defects and meet the necessary specifications.
The Significance Of Welding Inspection:
- Welding inspection is a critical aspect of any welding project as it ensures the quality and safety of the welds.
- It involves examining the welds to identify potential defects and ensure compliance with industry standards and specifications.
- The main purpose of welding inspection is to detect any flaws or defects early on, allowing for timely repairs and preventing costly rework or failures.
- It plays a crucial role in maintaining the structural integrity and reliability of welded components and structures.
- Welding inspection also helps in assessing the skill level of welders and ensuring adherence to proper welding techniques.
Common Welding Defects And How To Prevent Them:
- Several common welding defects can compromise the integrity and quality of welds. Some of these defects include:
- Porosity: This occurs when gas bubbles get trapped in the weld, resulting in weakened joints. To prevent porosity, it is important to properly clean and prepare the base material, use clean filler material, and maintain proper shielding gas coverage.
- Lack of fusion: This defect occurs when there is inadequate bonding between the base metal and the filler metal, resulting in weak or incomplete welds. To prevent a lack of fusion, it is essential to ensure proper joint fit-up, adequate heat input, and proper welding technique.
- Cracking: Weld cracking can occur due to various factors such as high stress levels, improper cooling, or hydrogen embrittlement. To prevent cracking, it is important to control the welding parameters, preheat the base material if necessary, and use low hydrogen electrodes or filler wire.
- Undercutting: This defect occurs when the weld metal erodes the base metal, resulting in a groove or depression along the weld. To prevent undercutting, it is crucial to maintain proper welding techniques, control the heat input, and use appropriate welding parameters.
Ensuring Quality Control In Welding Projects:
- Quality control is an essential aspect of welding projects to ensure that the finished welds meet the required standards and specifications. Some key practices for ensuring quality control in welding projects include:
- Material inspection: Thoroughly inspect the base materials for any defects, such as cracks, pitting, or contamination, before starting the welding process.
- Welding procedure qualification: Establish and qualify welding procedures to ensure consistency and quality in each weld. This involves testing and documenting the welding parameters, joint preparation, and welding technique.
- Welder qualification: Ensure that welders are properly trained, qualified, and certified for the specific welding processes and materials used in the project.
- In-process inspection: Regularly inspect the welds during the welding process to identify any defects or deviations from the specified requirements. This can be done through visual inspections, non-destructive testing, or other inspection methods.
- Final inspection: Conduct a final inspection after completing the welding process to ensure that all the welds meet the required standards and specifications.
- Documentation and record-keeping: Maintain accurate records of all inspections, test results, and certifications for future reference and quality assurance.
By implementing thorough welding inspection and quality control measures, welding projects can achieve high-quality and reliable welds, ensuring the safety and integrity of the finished products or structures.
Importance Of Welding Codes And Standards
Welding codes and standards play a crucial role in ensuring the quality and safety of welds. These guidelines provide the most important criteria for weld design, inspection, and performance, ensuring that welds meet industry standards and regulations. Adhering to these codes and standards is vital to prevent structural failures, ensure worker safety, and maintain overall welding efficiency.
Understanding Welding Codes And Standards:
- Welding codes and standards are a set of guidelines and specifications that must be followed in the welding industry. These codes ensure that welding is done safely, efficiently, and with high quality.
- Understanding welding codes and standards is crucial for welders, engineers, and inspectors to ensure the integrity and durability of welded structures.
- Welding codes provide information on various welding processes, techniques, materials, and quality requirements. They also cover safety protocols and testing procedures.
- By adhering to welding codes and standards, professionals can guarantee the structural soundness of their welds and adhere to industry best practices.
Complying With Industry Specifications And Regulations:
- Compliance with industry specifications and regulations is essential in welding to ensure that projects are completed to the highest standards.
- Industry specifications vary depending on the type of welding, materials being used, and the specific application.
- Compliance ensures that the welding process meets the required safety, quality, and performance criteria. It also helps in avoiding legal implications and liability issues.
- Welding projects that adhere to industry specifications and regulations are more likely to be approved by clients, regulators, and inspectors. It also enhances the reputation and credibility of the welder or company.
Benefits Of Adhering To Welding Codes And Standards:
- Adhering to welding codes and standards offers several benefits to both individuals and organizations involved in welding projects. These benefits include:
- Safety: Welding codes prioritize safety by providing guidelines for handling hazardous materials, preventing accidents, and implementing appropriate personal protective equipment (PPE).
- Quality: Following welding codes ensures that the welds are done to the required quality standards, resulting in strong and durable structures.
- Consistency: By maintaining consistency with welding codes and standards, the quality of welds remains consistent across different projects and locations.
- Compliance: Adhering to welding codes and standards ensures compliance with legal and regulatory requirements, avoiding penalties and liabilities.
- Customer Satisfaction: Meeting or exceeding welding codes and standards leads to customer satisfaction as it ensures the reliability and longevity of the welded structures.
- Professional Development: Staying updated with welding codes and standards allows welders to enhance their knowledge and skills, making them more competitive in the industry.
Welding Training And Education
The most important thing in welding is safety, specifically being educated about and aware of the risks of electric shock.
The Value Of Proper :
- Proper training and education are crucial in the welding industry to ensure safety, efficiency, and high-quality work.
- Training provides essential knowledge and skills in various welding techniques, equipment handling, safety protocols, and understanding different types of materials.
- With proper training, welders can learn the correct welding procedures, such as prepping materials, fitting and aligning components, and applying the appropriate heat and filler metal to create strong and durable welds.
- Education also includes theoretical aspects, such as understanding metallurgy, blueprint reading, codes, and standards, which are essential for producing welds that meet industry requirements.
- Effective training programs allow welders to practice these skills in a controlled environment, under the supervision of experienced instructors, to gain confidence and proficiency.
- Overall, proper welding training and education contribute to producing skilled and knowledgeable welders who can deliver high-quality work while prioritizing safety.
Career Opportunities In The Welding Industry:
- The welding industry offers a wide range of career opportunities, making it an attractive field for individuals interested in skilled trades.
- Skilled welders are in high demand across various industries such as construction, manufacturing, automotive, aerospace, oil and gas, and shipbuilding.
- Welding opens up opportunities for employment in different job roles, including welder fabricators, pipefitters, boilermakers, welding inspectors, welding engineers, and welding educators.
- With experience and additional certifications, welders can progress to supervisory or managerial positions, leading teams and overseeing welding projects.
- The demand for skilled welders is projected to remain strong in the coming years, providing stable and well-paying career options for those who pursue welding as a profession.
Continuous Learning To Stay Updated With Industry Advancements:
- The welding industry is constantly evolving, with new technologies, techniques, and materials emerging regularly.
- To stay competitive and meet industry demands, welders need to engage in continuous learning and professional development.
- Continuous learning allows welders to stay informed about the latest welding equipment, tools, and technologies, enabling them to work more efficiently and effectively.
- Industry advancements, such as automation and robotics in welding, require welders to upskill and adapt to new working methodologies and processes.
- Learning from experienced professionals, attending workshops, conferences, and industry events, and engaging in online resources and forums are effective ways to stay updated with industry advancements.
- By embracing continuous learning, welders can expand their knowledge, enhance their skills, and remain valuable assets to their employers, increasing their career prospects in the welding industry.
Welding Techniques For Different Applications
The most important thing in welding is safety. Welders need to be educated and aware of potential hazards, such as electric shock, to protect themselves while working in a hot work environment.
Read More: What are Three Important Skills under a Welder?
Welding is a versatile process that plays a vital role in various industries. Different welding techniques are used depending on the specific application and the materials involved. Understanding these techniques and their applications is crucial to ensure successful and high-quality welds.
Here are some key points to know about different welding techniques:
- Gas Metal Arc Welding (GMAW), also known as MIG welding, is commonly used for welding steel and non-ferrous materials. It is suitable for both thin and thick materials, making it versatile for a wide range of applications.
- Shielded Metal Arc Welding (SMAW), also known as stick welding, is a popular technique for outdoor and construction applications. It is commonly used for welding steel and cast iron, providing excellent penetration and strength.
- Gas Tungsten Arc Welding (GTAW), also known as TIG welding, is a precise technique that is commonly used for welding thin materials, such as stainless steel and aluminum. It produces high-quality welds with minimal spatter.
- Flux-Cored Arc Welding (FCAW) is a versatile technique that combines the benefits of both GMAW and SMAW. It is suitable for welding thick materials and can be used in various positions.
- Plasma Arc Welding (PAW) is a specialized technique commonly used in the aerospace and automotive industries. It provides precise control and is often used for welding intricate shapes and small components.
Choosing The Right Technique For The Task At Hand
Selecting the appropriate welding technique is crucial to ensure the desired outcome and efficiency in the welding process. Consider the following factors when choosing the right technique:
- Material type: Different materials require specific welding techniques to achieve optimal results. Consider the material’s composition, thickness, and properties before deciding on the technique to use.
- Joint configuration: The joint design and accessibility play a significant role in determining the most suitable welding technique. Ensure that the chosen technique can effectively weld the joint configuration.
- Weld quality requirements: Evaluate the desired weld quality, including factors such as strength, appearance, and structural integrity. Some techniques may be better suited to meet specific quality requirements.
- Application environment: Consider the environmental conditions in which the weld will be subjected, such as extreme temperatures, corrosion, or mechanical stress. Certain techniques offer better durability in specific environments.
- Skills and equipment availability: Assess the available welding equipment and the expertise of the welder. Some techniques may require specialized equipment or advanced skills.
Advancements In Welding Technology For Specific Industries
Various industries have specific welding needs, driving the development of advanced welding technology. Here are some notable advancements in welding technology for specific industries:
- Automotive industry: Laser welding and robotic welding systems have gained popularity in the automotive industry due to their precision, speed, and reliability. These technologies enable the production of high-quality and durable welds in automotive components.
- Aerospace industry: Electron beam welding (EBW) and friction stir welding (FSW) are widely used in the aerospace industry for their ability to produce strong, defect-free welds in high-performance materials such as titanium and aluminum alloys.
- Construction industry: In the construction sector, advancements have been made in welding technologies like stud welding and submerged arc welding (SAW). These techniques offer improved efficiency and productivity, making them ideal for large-scale construction projects.
- Energy industry: The energy sector, including oil and gas, relies on advanced welding techniques such as orbital welding and automated welding systems. These technologies ensure precise and reliable welds in critical components under extreme conditions.
- Medical industry: Laser beam welding and spot welding techniques are used in the medical industry for joining delicate and small components, such as medical devices and implants. These methods provide precise control and minimize heat-affected zones.
Choosing the right welding technique for different applications is essential for achieving high-quality welds. Advances in welding technology continue to drive innovation in specific industries, leading to improved efficiency, durability, and precision in the welding process.
The Future Of Welding
Ensuring proper safety measures and training for welders is the most important aspect of welding. Electric shock is a major concern that welders should be educated about to prevent immediate and serious risks. Focusing on safety precautions is crucial to protect both the welder and the work environment.
Welding, as a field, has been evolving and adapting to new technologies and trends. The future of welding holds exciting possibilities, including emerging trends and technologies, the impact of automation and robotics, and the importance of adapting to change in the welding industry.
Emerging Trends And Technologies In Welding:
- Laser welding: With its precise and focused heat source, laser welding offers numerous advantages, such as reduced distortion, increased welding speed, and enhanced control over the welding process.
- 3D printing in welding: This innovative technology allows for the creation of complex and intricate welds, offering greater design flexibility and cost-effective production.
- Virtual reality (VR) training: VR is revolutionizing the way welders are trained, providing an immersive and realistic environment for practice and skill development.
- Augmented reality (AR) in welding: AR can overlay digital information onto the welding process, providing real-time feedback, visualization of weld paths, and guidance to enhance accuracy and productivity.
- Nanotechnology in welding: Nanomaterials and nanocoatings are being used to improve the properties of welds, such as strength, durability, and corrosion resistance.
Impact Of Automation And Robotics On The Welding Industry:
- Increased productivity: Automation and robotics can perform repetitive and time-consuming tasks with precision and speed, leading to higher productivity and reduced labor costs.
- Enhanced safety: Robots can perform welding in hazardous environments or difficult-to-reach areas, reducing the risks associated with human welders.
- Consistent quality: Automation ensures consistent weld quality, minimizing errors and defects that may occur due to human factors.
- Workforce implications: While automation may replace some manual welding jobs, it also creates new opportunities for skilled workers to operate and maintain robotic welding systems.
The Importance Of Adapting To Change In The Welding Field:
- Continuous learning: As new technologies and techniques emerge, welders must stay updated and keep learning to remain competitive in the industry.
- Flexibility and versatility: Welders need to be adaptable and proficient in various welding processes, materials, and technologies to meet the changing demands of different projects.
- Embracing innovation: Being open to new ideas and embracing innovative solutions can lead to improved efficiency, cost-effectiveness, and overall performance in welding.
- Collaboration and networking: Connecting with other professionals in the welding field, attending conferences, and staying involved in industry associations can provide valuable insights and opportunities for professional growth.
Frequently Asked Questions On What Is The Most Important Thing In Welding?
What Is The Golden Rule In Welding?
The golden rule in welding is to maintain safety at all times. This includes wearing the appropriate protective gear, ensuring proper ventilation in the workspace, and following all safety protocols.
What Is The Main Rule Of Welding?
The main rule of welding is to always follow safety guidelines, including wearing appropriate protective gear and ensuring a clean and well-ventilated workspace.
What Is the Importance Of Welding?
In welding, the most important thing is the ability to handle various welding processes and metal materials efficiently, even in challenging conditions. Additionally, proper training, certifications, and knowledge of safety protocols are essential.
What Are Three Important Skills Under A Welder?
Three important skills under a welder include
1. Proficiency in various welding processes, such as MIG, TIG, and Stick.
2. Knowledge of different metal materials and their welding requirements.
3. Ability to weld in challenging conditions and tight spaces.
What Are The Three Most Important Welding Techniques?
– There are many different welding techniques, but three important ones are MIG welding, TIG welding, and Stick welding. These techniques each have their advantages and are suited for different types of projects.
Conclusion
In the world of welding, one may wonder what the most important thing is. While there are many factors to consider, one key aspect stands above the rest: training and experience. Welding is not just about joining metals together; it requires skill, precision, and a deep understanding of various welding processes and metal materials.
Whether it’s MIG, TIG, Stick, Pulse, or underwater welding, being knowledgeable in these techniques is crucial. Additionally, employers often value certifications and may even offer training opportunities or reimbursement for college courses. But it’s not just about technical expertise; a successful welder must also possess dedication and a keen eye for detail.
They must be able to work in challenging environments and practice their craft until it becomes second nature. Welding, after all, is a hot and bright job that requires focus and determination. So, while there are many important aspects to welding, investing in training and gaining experience sets a welder on the path to success.