In welding, Does 135 Mean in Welding? The number 135 typically refers to a specific welding process known as Gas Metal Arc Welding (GMAW). GMAW is a type of arc welding that uses a consumable electrode and a shielding gas to protect the weld from contaminants.
This process is commonly used in various industries for its versatility and ease of use. GMAW can be used on a wide range of materials and thicknesses, making it a popular choice among welders. Understanding the specific welding processes and their corresponding numbers is essential for welders to ensure they are using the correct techniques and equipment for each job.
Understanding Welding Process Numbers
Definition of Welding Process Numbers
Welding process numbers, also known as welding procedure numbers (WPS), are alphanumeric codes that represent different welding processes. These numbers provide standardized guidelines and specifications for welders to follow in order to ensure consistent and high-quality welds.
Each welding process has a unique welding process number assigned to it, which allows welders and industry professionals to easily identify and communicate the specific requirements for a particular welding job.
Importance of Welding Process Numbers in the Welding Industry
The use of welding process numbers is of utmost importance in the welding industry, as it ensures uniformity and compliance with welding standards and regulations. By adhering to the specified welding process number, welders can maintain consistency in their welding techniques, which ultimately results in the production of strong and reliable welds.
Additionally, welding process numbers promote safety by providing clear instructions and guidelines for welders to follow, minimizing the risk of welding defects and accidents.
Explanation of Different Welding Process Numbers
There are numerous welding process numbers that correspond to various welding techniques. Some common welding process numbers include gas metal arc welding (GMAW) represented by the number 135, gas tungsten arc welding (GTAW) represented by the number 141, and shielded metal arc welding (SMAW) represented by the number 111.
Each welding process number signifies a specific combination of welding parameters, such as the type of welding electrode or filler material, shielding gas, and welding current and voltage settings. This allows welders to understand the requirements and parameters for each welding process number and select the appropriate technique for a given welding application.
Welding Process Number 135
Welding process number 135, also known as gas metal arc welding (GMAW) or metal inert gas (MIG) welding, is a commonly used welding technique in various industries. In GMAW, a continuous consumable electrode is fed through a welding gun, while a shielding gas is used to protect the weld pool from atmospheric contamination.
This welding process number is particularly effective for joining thin to medium-thickness metals and offers high deposition rates, making it suitable for both fabrication and repair work. Welders using process number 135 should be knowledgeable about the specific welding parameters and techniques associated with this process to ensure successful welds.
Brief Overview of Other Common Welding Process Numbers
Aside from welding process number 135, several other welding process numbers are commonly used in the welding industry. These include:
- Process number 141 (GTAW/TIG welding): Used for precise and high-quality welding of thin metals, and commonly employed in industries such as aerospace and automotive.
- Process number 111 (SMAW/stick welding): A versatile welding technique suitable for welding a wide range of metals, including steel, stainless steel, and cast iron.
- Process number 136 (Flux-cored arc welding): Combines the benefits of both GMAW and SMAW and is often used for welding thick materials and in outdoor or windy conditions.
These are just a few examples of welding process numbers, each representing a unique set of welding parameters and techniques. By understanding the characteristics and applications of different welding process numbers, welders can make informed choices for their specific welding projects.
Exploring Gas Metal Arc Welding (Gmaw)
Introduction to Gas Metal Arc Welding
Gas Metal Arc Welding (GMAW), also known as Metal Inert Gas (MIG) welding, is a widely used welding process in industries around the world. It involves the use of a continuous consumable electrode, typically a solid wire, along with a shielding gas to protect the weld area from atmospheric contamination.
GMAW offers several advantages over other welding processes, which makes it a popular choice for various applications.
Brief Explanation of the GMAW Process
In GMAW, a power source supplies a constant voltage or current to the welding gun, which controls the wire feed speed. The wire is continuously fed into the arc, melting and depositing molten metal into the joint.
The shielding gas, usually a mixture of carbon dioxide and argon, or pure argon for non-ferrous materials, is directed through the welding gun to prevent oxidation and ensure a high-quality weld. GMAW can be performed in a variety of positions, making it versatile in various welding scenarios.
Advantages and Disadvantages of GMAW
GMAW offers several advantages that make it a popular choice in the welding industry. Some of these advantages include:
- High deposition rates
- Good control over the welding process
- Can be used with different materials and thicknesses
- Produces clean and visually appealing welds
- Minimal post-weld cleaning required
However, GMAW also has its disadvantages, such as:
- Higher equipment cost compared to other welding processes
- Sensitivity to wind and drafts due to the reliance on a shielding gas
- Not suitable for outdoor applications where wind is a factor
Applications and Industries Where GMAW is Commonly Used
GMAW is commonly used in various industries and applications due to its versatility and efficiency. Some of these industries include:
- Automotive manufacturing
- Shipbuilding
- Aerospace
- Construction
- General Fabrication
Its ability to weld a wide range of materials, from steel to aluminum, and its ease of use make it a popular choice in these industries.
Understanding the Relationship Between Welding Process Number 135 and GMAW
Welding process number 135 refers to the specific designation given to gas metal arc welding (GMAW) in the classification system for welding processes. This number helps in identifying the welding process and its parameters, ensuring that industry standards and specifications are met. So, when you hear or see the term 135 in welding, it refers to GMAW and its associated techniques and guidelines.
Factors Affecting Welding Process Number 135
Understanding Voltage & Amperage in Welding
When it comes to welding, voltage, and amperage play a crucial role in determining the quality of the weld. Amperage measures the strength of the electrical current used during a weld, while voltage measures the pressure of the current. Understanding these two factors is essential for achieving the desired results in welding.
How Voltage & Amperage Affect the Welding Process
Voltage and amperage directly affect the heat input and arc length, which in turn affect the penetration and overall quality of the weld. In general, higher voltage and amperage settings result in greater heat input, deeper penetration, and faster deposition rates.
On the other hand, lower voltage and amperage settings will produce less heat input, shallower penetration, and slower deposition rates. It’s important to find the right balance between voltage and amperage to ensure the desired weld characteristics.
Exploring the Ideal Voltage & Amperage Settings for Welding Process Number 135
When it comes to welding process number 135, which refers to the Shielded Metal Arc Welding (SMAW) process, finding the ideal voltage and amperage settings is crucial. SMAW is a widely used welding process that utilizes a flux-covered electrode to create an arc.
To determine the appropriate voltage and amperage settings for SMAW welding, factors such as electrode size, base metal thickness, joint configuration, and welding position need to be considered. A higher voltage and amperage setting may be required for thicker materials or larger electrode sizes, while lower settings may be suitable for thinner materials.
It is important to refer to the welding procedure specifications (WPS) provided by the manufacturer or consult with a welding engineer to determine the specific voltage and amperage settings for welding process number 135. Following the recommended settings will help ensure a successful weld with proper penetration and strength.
Techniques And Best Practices For Welding Process Number 135
Welding Process Number 135, also known as Gas Metal Arc Welding (GMAW) or Metal Inert Gas (MIG) welding, is a popular and widely used welding technique that allows for efficient and high-quality welds. To ensure successful welds, following proper techniques and best practices is important. In this article, we will discuss the preparation and setup, equipment and material selection, proper welding techniques, and safety precautions for Welding Process Number 135.
Preparation and Setup for Welding Process Number 135
Effective preparation and setup are crucial for achieving quality welds with Welding Process Number 135. Here are some key steps to follow:
- Ensure the workpiece is clean, and free from dirt, rust, and other contaminants. Clean the surface using a wire brush or other suitable cleaning methods.
- Position the workpiece securely, ensuring it is stable and properly aligned. Use clamps or fixtures if necessary.
- Set up a welding area with proper ventilation to prevent the accumulation of hazardous fumes or gases.
- Inspect and adjust the welding equipment, including the welding machine, wire feeder, and shielding gas supply, to ensure they are in good working condition.
Selection of Appropriate Equipment and Materials
Choosing the right equipment and materials is essential for successful Welding Process Number 135. Consider the following factors when making your selection:
- Select a suitable welding machine with the right power output and voltage capabilities for the intended application.
- Choose the appropriate wire feeder and welding gun that are compatible with the welding machine.
- Consider the type and thickness of the base metal to determine the appropriate welding wire and shielding gas.
- Ensure you have the necessary safety equipment and personal protective gear, such as welding helmets, gloves, and protective clothing.
Proper Welding Techniques for Achieving High-Quality Welds
Mastering the proper welding techniques is crucial for achieving high-quality welds with Welding Process Number 135. Here are some essential techniques to follow:
- Maintain the correct electrode extension and travel speed to ensure proper fusion and penetration.
- Use the appropriate welding technique, such as a push or pull technique, based on the welding position and joint configuration.
- Maintain a consistent arc length and angle to control the heat input and prevent excessive spatter.
- Control the wire feed speed and voltage settings to achieve the desired weld bead size and shape.
Safety Precautions and PPE Requirements for Welding Process Number 135
Ensuring safety during Welding Process Number 135 is paramount. Here are some important safety precautions and personal protective equipment (PPE) requirements:
- Always wear a welding helmet with the appropriate shade of lens to protect your eyes from harmful ultraviolet (UV) and infrared (IR) radiation.
- Use welding gloves to protect your hands from burns and sparks.
- Wear flame-resistant clothing, such as welding jackets, pants, and aprons, to protect against heat and sparks.
- Wear ear protection to safeguard against excessive noise levels.
- Ensure proper ventilation in the welding area to prevent the accumulation of hazardous fumes and gases.
By following these techniques and best practices, you can achieve high-quality welds and ensure a safe working environment when using Welding Process Number 135.
Troubleshooting And Common Challenges In Welding Process Number 135
Common issues and challenges faced in welding process number 135
Welding process number 135, also known as Gas Metal Arc Welding (GMAW), is a commonly used welding method in various industries. While it offers numerous advantages such as high welding speed and efficiency, easy automation, and versatility, there are some common challenges that welders may encounter during the process.
1. Porosity: One of the most common issues in GMAW is the formation of porosity in the weld. Porosity occurs when gas bubbles are trapped in the weld metal, leading to reduced strength and integrity. This can be caused by factors such as improper shielding gas flow, contaminated base metal, or improper cleaning of the joint surface.
2. Incomplete fusion: Incomplete fusion happens when the weld metal fails to fuse completely with the base metal or previous layers. This can result in weak and unreliable welds. It can be caused by factors such as inadequate heat input, improper joint preparation, or insufficient welding technique.
3. Weld spatter: Weld spatter refers to the small droplets of metal that can be ejected during the welding process and can lead to surface imperfections and inconsistent weld quality. Factors contributing to excessive spatter include high current settings, improper wire feed speed, or inadequate shielding gas coverage.
4. Cracking: Cracking can occur in the weld or surrounding base metal and can lead to weld failure. It can be caused by factors such as high cooling rates, inadequate preheating, or improper selection of filler material.
5. Inconsistent weld bead: GMAW may produce inconsistent weld bead appearance, which can impact the overall aesthetics and functionality of the weld. This can be caused by factors such as improper travel speed, erratic wire feed, or insufficient shielding gas coverage.
Tips for troubleshooting and resolving welding process number 135 problems
When facing challenges in the GMAW process, it is essential to identify and address the underlying issues to ensure successful welds. Here are some tips for troubleshooting and resolving common problems in welding process number 135:
- Ensure proper shielding of gas flow and coverage by checking gas flow meters and adjusting gas regulators accordingly.
- Thoroughly clean and prepare the joint surfaces, removing any contaminants or oxides, to promote better fusion and minimize porosity.
- Optimize heat input by adjusting the voltage and wire feed speed to achieve proper penetration and fusion.
- Select the appropriate filler material and electrode for the specific application and base metal to prevent cracking and achieve desired weld properties.
- Maintain consistent travel speed and wire feed, ensuring smooth and uniform bead appearance.
- Regularly inspect equipment, including welding guns, contact tips, and nozzles, and replace or repair any worn or damaged parts that may contribute to welding issues.
- Monitor and control heat input and cooling rates to minimize distortion and prevent cracking.
- Perform post-weld inspections, such as visual examinations, to identify defects or imperfections and take corrective measures as necessary.
Prevention strategies for avoiding common welding defects in process number 135
While troubleshooting and resolving welding issues is crucial, prevention is always better than cure. By implementing certain strategies, welders can minimize the occurrence of common defects in GMAW:
- Adhere to proper joint preparation techniques, ensuring adequate cleaning, beveling, and fit-up to promote better fusion and minimize defects.
- Establish appropriate welding parameters, including voltage, wire feed speed, and shielding gas flow, based on material thickness and composition.
- Implement proper gas shielding techniques, such as maintaining the correct distance between the nozzle and workpiece, to ensure complete coverage and minimize porosity.
- Utilize proper filler materials and electrodes based on material compatibility and desired weld properties.
- Regularly maintain and calibrate welding equipment to ensure consistent and reliable performance.
- Train and educate welders on proper welding techniques, including travel speed, weaving patterns, and manipulation, to achieve consistent and high-quality welds.
- Implement quality control measures, such as visual inspections, non-destructive testing, and welder qualification, to detect and address defects early on.
By troubleshooting welding issues, implementing effective troubleshooting strategies, and following prevention techniques, welders can overcome common challenges in welding process number 135 and achieve high-quality welds with improved efficiency.
Comparison Of Welding Process Number 135 With Other Welding Processes
Comparison of Welding Process Number 135 with Other Welding Processes
When it comes to welding, there are various techniques and processes available, each with its own advantages and disadvantages. One such welding process is 135, also known as Gas Metal Arc Welding (GMAW) or Metal Inert Gas (MIG) welding. In this section, we will compare process number 135 with other gas metal arc welding processes, highlight its advantages and disadvantages, and explore applications where other welding processes may be more suitable.
Comparison of Welding Process Number 135 with Other Gas Metal Arc Welding Processes
Gas Metal Arc Welding (GMAW) Process
The 135 welding process falls under the broader category of gas metal arc welding, which includes other processes such as 123, 136, and 138. These processes differ in terms of the electrical and shielding gas characteristics used.
Process 135 involves the use of a solid wire electrode and a shielding gas mixture of argon and carbon dioxide, commonly referred to as C25 gas. This combination provides excellent penetration, efficient metal transfer, and reduces the risk of weld spatter.
Advantages and Disadvantages of Welding Process Number 135 Compared to Other Processes
Advantages of Welding Process Number 135
- Highly versatile, suitable for welding a wide range of materials, including stainless steel, carbon steel, and aluminum.
- Easy to learn and use, making it ideal for beginners.
- Provides good control over the welding process, allowing for precise weld bead formation.
- Efficient and productive, enabling faster welding speeds and high deposition rates.
- Less sensitive to wind or drafts compared to other processes.
Disadvantages of Welding Process Number 135
- Requires the use of shielding gas, which adds to the overall cost of welding.
- Suitable for thinner materials, limiting its application in heavy-duty welding tasks.
- Not ideal for outdoor welding due to the need for shielding gas.
- Prone to porosity if proper gas coverage is not maintained.
Applications and Scenarios Where Other Welding Processes May be More Suitable than Process Number 135
Process 123
123 welding process is preferred for applications that involve welding thin materials, as it offers better control over the heat input and reduces the risk of distortion.
Process 136
136 welding process, also known as Dual Shield welding, is commonly used for welding thick materials or in outdoor environments. It utilizes a flux-cored wire electrode, providing better penetration and higher deposition rates compared to process 135.
Process 138
138 welding process, also known as Metal Cored Arc Welding, is suitable for applications that require high-quality welds in thicker materials. It combines the advantages of both solid wire and flux-cored wire electrodes, offering increased efficiency and higher productivity.
Professional Welding Certification And Training For Welding Process Number 135
When it comes to welding, having the proper training and certification is crucial. One specific welding process that requires specialized knowledge and expertise is welding process number 135. This process, also known as Gas Metal Arc Welding or GMAW, is commonly used in various industries for its efficiency and versatility.
Importance of proper training and certification for welding process number 135
Proper training and certification play a significant role in ensuring the safety and success of welding process number 135. Here are some reasons why it is important:
- Minimize the risk of accidents and injuries: Welding involves working with high temperatures and potentially hazardous materials. With the right training, welders can learn safety protocols, hazard recognition, and proper handling techniques to prevent accidents and injuries.
- Ensure quality and precision: Welding process number 135 requires precise techniques to achieve strong and reliable welds. Proper training and certification help welders develop the necessary skills to produce high-quality welds that meet industry standards consistently.
- Compliance with industry regulations: Many industries have strict regulations and standards for welding processes. By obtaining the appropriate certifications, welders can demonstrate their compliance with these regulations, increasing their employability and credibility.
Overview of relevant certifications and qualifications for welding process number 135
Acquiring the right certifications and qualifications is essential for welders specializing in welding process number 135. Here are some certifications that are highly regarded in the industry:
Certification | Description |
---|---|
American Welding Society (AWS) Certified Welder | This certification validates a welder’s skills and knowledge in various welding processes, including GMAW. It involves a combination of written examinations and practical welding tests. |
Canadian Welding Bureau (CWB) Certification | The CWB certification is recognized in Canada and signifies a welder’s competence in specific welding processes, including GMAW. It requires both theoretical and practical assessments. |
European Welding Federation (EWF) Diploma | The EWF diploma is an internationally recognized qualification that demonstrates a welder’s proficiency in a range of welding processes, including GMAW. It involves comprehensive theoretical and practical examinations. |
Options for acquiring necessary skills and certifications in welding process number 135
For aspiring welders looking to acquire the necessary skills and certifications in welding process number 135, there are several options available:
- Technical schools and vocational training centers: Many educational institutions offer specialized welding programs that cover GMAW and other welding processes. These programs provide a combination of theoretical knowledge and practical hands-on training.
- Apprenticeships: Apprenticeship programs allow individuals to learn from experienced welders while gaining practical on-the-job training. These programs typically require a certain number of hours of supervised work and may lead to certification.
- Professional welding organizations: Organizations like the American Welding Society and the Canadian Welding Bureau offer certification programs and resources for welders. They often provide training courses, workshops, and study materials to assist aspiring welders in obtaining the necessary qualifications.
By investing in proper training and certification, welders can enhance their career opportunities and demonstrate their expertise in welding process number 135. Whether through educational institutions, apprenticeships, or professional organizations, the path to becoming a certified welder in GMAW is achievable and rewarding.
Advancements And Future Trends In Welding Process Number 135
Innovations and Advancements in Welding Process Number 135
Welding process number 135, also known as Gas Metal Arc Welding (GMAW), has seen significant innovations and advancements in recent years. This welding process involves using a continuous consumable electrode and shielding gas, making it highly efficient and versatile.
One of the key advancements in GMAW is the development of new variations of the process, such as pulsed GMAW and spray GMAW. Pulsed GMAW provides better control over the heat input, resulting in improved weld quality and reduced distortion. On the other hand, spray GMAW allows for higher deposition rates, making it ideal for heavy fabrication and production welding.
Furthermore, advancements in welding power sources and wire feeder technology have made GMAW more user-friendly and efficient. The introduction of intelligent control systems has improved weld consistency and reduced the need for manual adjustments, enhancing productivity and reducing the chance of human error.
Emerging Technologies and Techniques Related to Welding Process Number 135
The future of welding process number 135 looks promising, with several emerging technologies and techniques set to revolutionize the industry. One of these innovations is the integration of robotics and automation into GMAW. Automated systems can perform precise and repetitive welding tasks with greater speed and accuracy than human welders, increasing efficiency and reducing costs.
Another emerging trend is the use of advanced welding consumables, such as high-strength filler wires and specialized shielding gases. These consumables are designed to improve weld quality and performance, especially in critical applications where strength and durability are crucial.
Additionally, the development of advanced sensing and monitoring technologies will enable real-time quality control and process optimization. Sensors can detect deviations in welding parameters and automatically adjust them to ensure consistent and defect-free welds. This level of automation and quality control will significantly improve productivity and reduce the need for post-weld inspections and rework.
Predictions for the Future of Welding Process Number 135 and Its Impact on the Industry
The future of welding process number 135 is bright, with several predictions for its continued growth and impact on the industry. With the constant advancements in technology, GMAW will become even more efficient, precise, and versatile.
Increased integration of artificial intelligence and machine learning algorithms will further enhance process control and optimization. Intelligent welding systems will be able to analyze vast amounts of data in real time, making autonomous decisions to maximize efficiency and productivity.
Moreover, the adoption of GMAW in various industries, including automotive, aerospace, and construction, is expected to grow rapidly. The process offers excellent weld quality and is well-suited for both heavy fabrication and intricate applications. This increased demand will drive further innovations and improvements in GMAW equipment and consumables.
In conclusion, welding process number 135, or GMAW, is continuously evolving, thanks to advancements in technology and the ever-increasing demand for efficient and high-quality welding solutions. As emerging technologies and techniques continue to shape the industry, it is clear that GMAW will play a significant role in the future of welding.
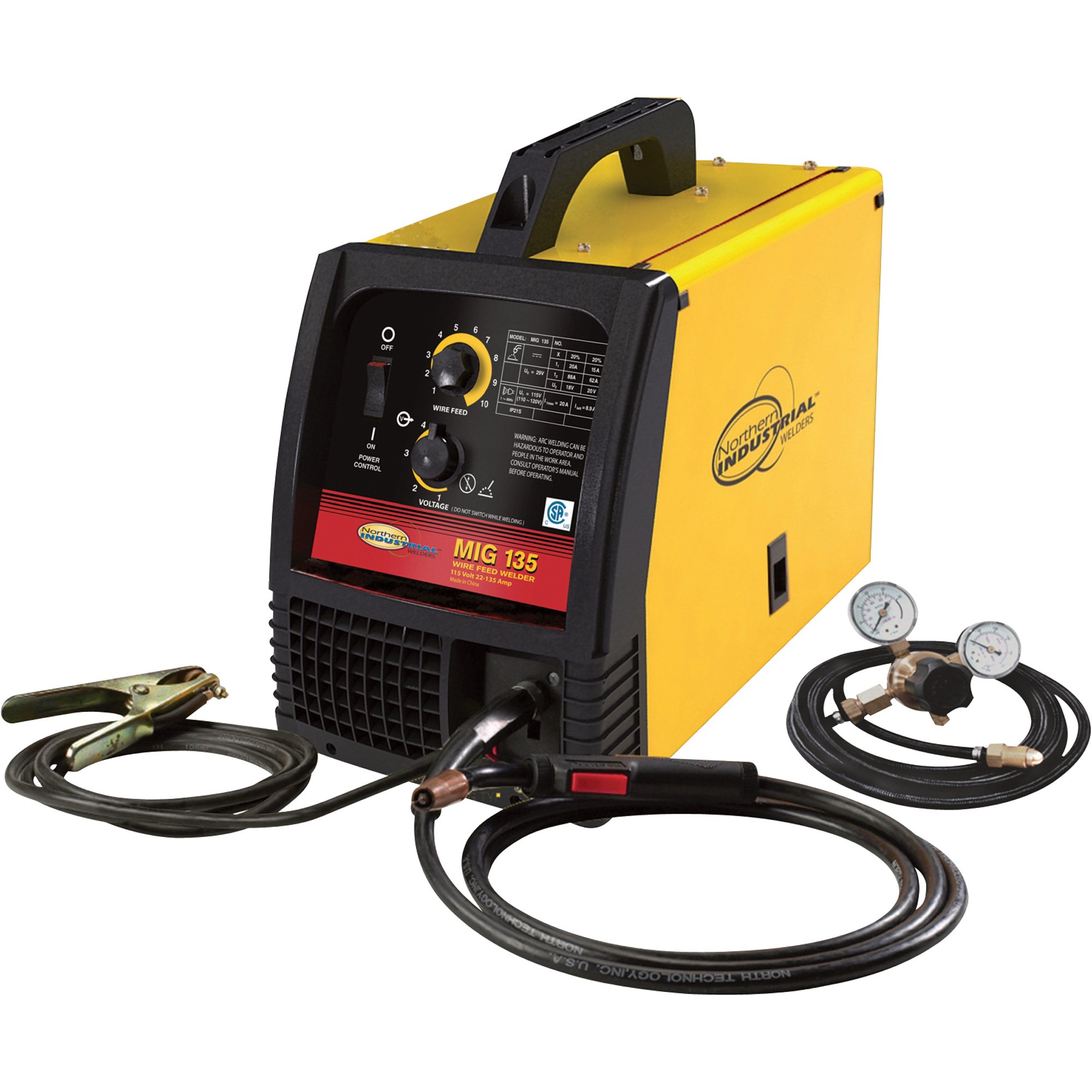
Credit: www.northerntool.com
Frequently Asked Questions On What Does 135 Mean In Welding?
What Is 136 Welding Code?
The 136 welding code refers to a specific welding process used in industry. It is categorized under Gas Metal Arc Welding (GMAW) or MIG (Metal Inert Gas) welding. This process involves using a continuous consumable electrode and shielding gas to join metals together.
What Is the 138 Welding Method?
The 138 welding method is not a recognized welding process.
What Does 141 Mean In Welding?
In welding, 141 refers to the welding process known as Gas Tungsten Arc Welding (GTAW), also commonly known as Tungsten Inert Gas (TIG) welding. GTAW uses a non-consumable tungsten electrode and an inert gas as the shielding gas to protect the weld from contamination.
What Is 111 In Welding?
111 in welding refers to the type of welding process called Gas tungsten arc welding (GTAW). GTAW uses a tungsten electrode to create an arc and a shielding gas to protect the weld from air contamination. This process is commonly used for high-quality welds on thin materials and for precise welding applications.
What Is The Significance Of The Number 135 In Welding?
The number 135 in welding refers to a specific welding process known as shielded metal arc welding (SMAW) with a specific size of electrode.
Conclusion
To conclude, understanding what 135 means in welding is essential for welders. It refers to the amperage setting on a welder, measuring the strength of the electrical current used during a weld. This knowledge helps welders determine the appropriate settings for different materials and thicknesses, ensuring high-quality and efficient welding results.
By mastering this concept, welders can enhance their skills and produce exceptional welds. So, remember to consider the significance of 135 in welding and apply it to your welding projects for optimal outcomes.