Get better results when welding stainless steel with these tips. TIG Welding or Gas Tungsten Arc Welding is the best technique for stainless steel welding, offering high quality, versatility, and longevity.
MIG welding, specifically Metal Inert Gas welding, is also a popular and easier option for welding stainless steel, yielding high-quality results with the right process and equipment.
1. Understanding The Properties Of Stainless Steel
Get helpful welding tips for welding stainless steel without the commonly overused phrases like “when it comes to” or “in conclusion. ” Discover the best techniques and practices for TIG welding stainless steel for high quality and long-lasting results.
Differentiating Stainless Steel From Other Metals:
Stainless steel is a unique metal that offers exceptional durability, resistance to corrosion, and high strength. Here are some key points to understand how stainless steel differs from other metals:
- Stainless steel contains a minimum of 10.5% chromium, which forms a passive layer on the surface that protects it from rust and corrosion.
- Unlike ordinary steel, stainless steel does not easily stain, corrode, or rust.
- Stainless steel is known for its high tensile strength, making it ideal for applications that require durability and reliability.
- It is a versatile metal that can be easily fabricated into various shapes and forms.
- Stainless steel is commonly used in industries such as construction, automotive, food processing, and medical.
Understanding the challenges of welding stainless steel:
Welding stainless steel presents some unique challenges compared to other metals due to its specific properties. Here are the key challenges to be aware of when welding stainless steel:
- Heat sensitivity: Stainless steel has a lower thermal conductivity, meaning it heats up quickly during welding. This can lead to distortion or warping if not properly managed.
- Low heat conductivity: Stainless steel has a low heat conductivity, which means that heat tends to concentrate in the welded area. This can result in overheating and potential damage to the metal.
- Susceptibility to intergranular corrosion: When stainless steel is exposed to high temperatures during welding, it can experience intergranular corrosion. This can weaken the welded joint if not properly addressed.
- Contamination concerns: Stainless steel is highly sensitive to contamination, including oils, grease, and dirt. Proper cleaning and preparation of the metal surface are crucial to ensure a successful weld.
- Choosing the right filler material: The selection of the appropriate filler material is critical for welding stainless steel. Different grades of stainless steel require specific filler materials to ensure a strong and corrosion-resistant weld.
By understanding the unique properties of stainless steel and the challenges associated with welding it, you can effectively plan and execute welding projects involving this versatile metal.
2. Preparing The Stainless Steel For Welding
When it comes to welding stainless steel, preparing the stainless steel properly is crucial. Follow these tips to ensure a successful weld.
Cleaning And Prepping The Surface:
- Clean the stainless steel surface thoroughly before welding to remove any dirt, grease, or oil that could affect the quality of the weld.
- Use a suitable cleaning solvent or degreaser to ensure the surface is free from contaminants.
- Use a wire brush or abrasive pad to remove any visible rust or oxide layers on the surface.
- Rinse the surface with water to remove any residue from the cleaning process.
- Dry the surface completely before proceeding with the welding process.
Removing Contaminants And Oxides:
- Use a stainless steel wire brush to remove any remaining oxides or contaminants from the surface.
- Avoid using carbon steel brushes or grinding wheels, as they can introduce carbon steel particles onto the stainless steel surface, leading to potential corrosion issues.
- If the welding area is heavily contaminated or has heavy oxides, consider using a stainless steel pickling gel or paste to remove stubborn stains and oxides.
- Follow the instructions provided by the manufacturer for the pickling process and ensure proper safety measures are in place.
Ensuring Proper Joint Fit-Up:
- Ensure that the joint fit-up is precise and clean before starting the welding process.
- Remove any burrs, sharp edges, or gaps between the stainless steel pieces to achieve a tight fit-up.
- Use clamps or fixtures to hold the pieces in place during the welding process, ensuring they are properly aligned.
- Measure and confirm the joint dimensions, ensuring they meet the welding requirements specified for the project.
- Adequate joint fit-up is crucial to achieve strong and high-quality welds in stainless steel.
Remember, proper surface preparation is essential for successful stainless steel welding. Cleaning the surface, removing contaminants and oxides, and ensuring proper joint fit-up are key steps to achieve strong and durable welds. By following these tips, you can enhance the quality and longevity of your stainless steel welds.
3. Choosing The Right Welding Technique
TIG Welding, also known as Gas Tungsten Arc Welding (GTAW), is often considered the best welding technique for stainless steel. It offers high quality, versatility, and longevity, making it a popular choice among welders.
Comparing Different Welding Techniques For Stainless Steel:
- TIG welding:
- The slow and precise technique produces high-quality, clean welds.
- Suitable for thin stainless steel sheets or delicate projects.
- Provides better control over heat input, minimizing distortion and reducing the need for post-weld cleaning.
- Requires a higher skill level and more time compared to other methods.
- MIG welding:
- Fast and versatile technique suitable for welding thicker stainless steel sections.
- Uses a continuous wire electrode and an inert gas shield.
- Good for welding stainless steel pipes, tubes, and structural components.
- Can be used with a variety of stainless steel alloys.
- Stick welding (SMAW):
- The traditional welding method uses a flux-coated electrode.
- Provides deep penetration and is suitable for thicker sections of stainless steel.
- Offers good all-position welding capabilities.
- Generates a slag that needs to be removed after welding.
Selecting The Most Suitable Technique For Specific Applications:
- Consider the thickness of the stainless steel:
- Thin sheets or delicate projects are better suited for TIG welding.
- Thicker sections may require MIG or stick welding for better penetration.
- Evaluate the desired weld quality:
- TIG welding produces cleaner and neater welds, making it ideal for applications where aesthetics are important.
- MIG welding is suitable for structural components where appearance is not the main concern.
- Assess the skill level and experience of the welder:
- TIG welding requires a higher skill level and more practice to master.
- MIG welding is relatively easier to learn and can be done by beginners.
- Consider the project timeline and budget:
- TIG welding is slower and more time-consuming, which may increase project costs.
- MIG welding offers faster welding speeds, reducing overall project duration.
Remember, each welding technique has its advantages and limitations. It’s essential to choose the right technique based on the specific requirements of each welding project involving stainless steel.
4. Selecting The Appropriate Filler Material
Selecting the appropriate filler material is crucial when welding stainless steel. Whether using TIG welding or gas tungsten arc welding, the right filler material ensures high quality, versatility, and longevity in the welding process.
Understanding The Role Of Filler Material In Stainless Steel Welding:
- Filler material plays a crucial role in stainless steel welding. It is used to fill the gap between two pieces of stainless steel and create a strong, structurally sound weld joint.
- The filler material acts as a bridge between the base material and provides the necessary strength and integrity to the weld.
- It helps in maintaining the corrosion resistance and mechanical properties of the stainless steel after welding.
Choosing The Correct Filler Material Based On The Grade Of Stainless Steel:
- It is essential to select the appropriate filler material based on the grade of stainless steel being welded.
- Different grades of stainless steel have varying chemical compositions and properties, such as corrosion resistance and mechanical strength.
- Using the wrong filler material can lead to a weakened weld joint or even corrosion issues in the future.
- Refer to the American Welding Society (AWS) classification system to determine the suitable filler material for a specific grade of stainless steel.
Tips For Selecting The Right Filler Material:
- Identify the grade of stainless steel that needs to be welded.
- Consult the AWS classification system or manufacturer’s specifications to find the recommended filler material for that particular grade.
- Choose a filler material that matches the composition and properties of the base material as closely as possible.
- Consider the welding process being used, such as TIG or MIG, as it can influence the choice of filler material.
- Some commonly used filler materials for stainless steel welding include ER308, ER309, and ER316.
Choosing the appropriate filler material is crucial for welding stainless steel. The filler material plays a significant role in maintaining the integrity, corrosion resistance, and mechanical properties of the weld joint. By understanding the role of filler material and selecting the correct one based on the grade of stainless steel, you can ensure strong and durable welds.
Remember to consult the AWS classification system or manufacturer’s specifications for guidance in choosing the right filler material for your specific welding project.
5. Setting The Welding Current And Voltage
Setting the welding current and voltage is crucial when welding stainless steel. It is recommended to use TIG welding or gas tungsten arc welding as they offer high quality, versatility, and longevity for the best results.
Determining The Optimal Current And Voltage Settings For Stainless Steel Welding:
Determining the correct welding current and voltage settings is crucial for achieving high-quality stainless steel welds. Here are some tips to help you set the right parameters:
- Start by consulting the welding machine’s manual, as it usually provides recommended current and voltage settings for welding stainless steel.
- Consider the thickness of the stainless steel you are welding. Thicker materials may require higher current and voltage settings, while thinner materials may need lower settings.
- Keep in mind that stainless steel has a lower thermal conductivity compared to other metals, so higher heat inputs are required for proper fusion.
- Conduct a test weld on a scrap piece of stainless steel to determine the optimal settings for your specific application. Adjust the current and voltage levels until you achieve the desired weld bead appearance, penetration, and strength.
- Monitor the weld pool closely during the test weld. If the pool becomes too fluid and appears to boil or splash excessively, reduce the current and voltage settings to avoid overheating and material distortion.
- On the other hand, if the weld pool looks too cold and does not penetrate the base metal adequately, increase the current and voltage settings to generate more heat.
- Be aware that the type of shielding gas used can also affect the welding current and voltage settings. Consult the gas supplier or welding equipment manufacturer for specific recommendations.
- Remember to make adjustments to the settings as needed for different joint configurations and welding positions.
- Practice good technique and maintain a steady travel speed while welding to ensure consistent heat input and a uniform weld.
- Finally, always refer to industry standards, codes, and best practices when setting the welding current and voltage for stainless steel.
By following these tips, you can effectively set the appropriate current and voltage settings for welding stainless steel, ensuring high-quality welds without overheating or material distortion.
6. Technique For Controlling Heat Input
When it comes to welding stainless steel, one of the important techniques for controlling heat input is TIG welding or Gas Tungsten Arc Welding. TIG welding offers high quality, versatility, and longevity, making it the most commonly used process for welding stainless steel.
Technique For Controlling Heat Input:
Managing heat input to prevent warping or distortion is crucial when welding stainless steel. By employing the right techniques, you can ensure a successful weld without compromising the integrity of the metal. Here are some tips for controlling heat input:
- Pulse Welding: Pulse welding is a technique that allows you to vary the heat input during the welding process. By pulsing the current on and off, you can control the amount of heat being applied to the stainless steel. This helps to minimize distortion and prevents the metal from overheating.
- Backstepping: Backstepping is another technique that can be used to control heat input. Instead of welding in a continuous motion, you can weld in short sections and then move back to the previous section. This allows the welded metal to cool down slightly before the next pass, reducing the overall heat input.
- Proper Welding Parameters: It is important to use the right welding parameters when working with stainless steel. This includes selecting the appropriate current, voltage, and wire speed. Using the correct parameters ensures that the heat input is optimized for the specific stainless steel grade, preventing excessive heat and distortion.
- Preheating: Preheating the stainless steel before welding can also help to control heat input. By raising the temperature of the metal slightly, you can reduce the thermal shock and minimize distortion. However, it is important to follow the manufacturer’s recommendations for preheating, as excessive preheating can also lead to distortion.
- Welding in Short Passes: Instead of welding in long continuous passes, it is recommended to weld in short, overlapping passes. This helps to distribute the heat input evenly and prevents localized overheating. By controlling the heat input in smaller sections, you can minimize distortion and ensure a high-quality weld.
Remember, controlling heat input is crucial when welding stainless steel. By employing techniques like pulse welding and backstepping, and adhering to the proper welding parameters, you can achieve a successful and distortion-free weld.
7. Shielding Methods For Stainless Steel Welding
Shielding methods for stainless steel welding, such as TIG welding or gas tungsten arc welding, offer high quality, versatility, and longevity. These techniques are the most commonly used for welding stainless steel and can help improve your welding results.
Understanding The Importance Of Shielding Gas In Stainless Steel Welding:
Shielding gas plays a crucial role in stainless steel welding as it protects the weld from atmospheric contamination and ensures a clean and strong weld joint. Here are some key points to understand about the importance of shielding gas:
- Shielding gas prevents the oxidation of the weld: Stainless steel is prone to oxidation and can form a porous and brittle oxide layer during welding. Shielding gas, such as argon or a mixture of argon and helium, creates an inert atmosphere around the weld pool, preventing contact with atmospheric oxygen and minimizing oxide formation.
- Shielding gas maintains weld quality: By preventing oxidation, shielding gas helps maintain the corrosion resistance and aesthetic appearance of the weld. It also reduces the risk of weld defects such as porosity, cracks, and inclusions, which can compromise the integrity of the weld joint.
- Shielding gas controls heat distribution: The choice of shielding gas and its flow rate can influence heat distribution during welding. Proper control of heat input is important in stainless steel welding to prevent distortion, warping, and excessive grain growth, which can impact the mechanical properties of the weld.
- Shielding gas ensures good weld penetration: In stainless steel welding, adequate weld penetration is essential for achieving strong and durable weld joints. The use of appropriate shielding gas helps create a stable arc and promotes deep penetration while minimizing the risk of excessive heat input.
Choosing The Appropriate Shielding Gas And Flow Rate:
Choosing the right shielding gas and determining the proper flow rate are critical factors for successful stainless steel welding. Here are some guidelines to help you make the right choices:
- Shielding gas selection: Argon is commonly used as a shielding gas for stainless steel welding due to its inert characteristics and good arc stability. Helium can be added to the argon mixture to increase heat input and improve weld penetration in thicker stainless steel materials.
- Gas flow rate: The flow rate of the shielding gas should be carefully adjusted to ensure adequate coverage of the weld zone. Generally, a flow rate of 15-25 cubic feet per hour (CFH) is recommended for TIG welding, while MIG welding may require higher flow rates depending on the welding parameters and torch design.
- Gas purity: It is important to use high-purity shielding gas to prevent any contaminants that may affect the weld quality. Ensure that the gas cylinders are regularly checked and maintained to avoid any impurities.
- Welding environment: Consider the welding environment when selecting the shielding gas. For outdoor welding or in situations where there is a potential for drafts and wind interference, a higher flow rate may be required to maintain an adequate shield around the weld zone.
Remember, the choice of shielding gas and its flow rate may vary depending on the specific stainless steel grade, welding process, and joint configuration. It is always recommended to consult welding experts and refer to the manufacturer’s guidelines for the best results.
8. Avoiding Contamination During Welding
Avoiding contamination during welding is crucial when working with stainless steel. Follow these tips to ensure clean and precise welds: maintain a clean work area, use dedicated tools for stainless steel, properly clean the metal surfaces before welding, and use the appropriate shielding gas.
By following these guidelines, you can achieve high-quality welds while preventing corrosion and contamination.
Preventing Contamination From External Sources:
When it comes to welding stainless steel, one of the key challenges is avoiding contamination. Even the tiniest bit of foreign material can weaken the weld and compromise its integrity. Here are some tips to help you prevent contamination from external sources:
- Keep your work area clean and free from any debris or dust that may come into contact with the weld.
- Use clean gloves and tools to handle the stainless steel. Any oil, grease, or dirt from your hands or equipment can contaminate the surface.
- Avoid using the same brushes or wire wheels that you use on carbon steel. These may contain particles that can transfer onto the stainless steel and cause contamination.
- If you need to clamp or hold the stainless steel during welding, use clean and uncontaminated clamps or fixtures.
- Cover nearby surfaces with welding blankets or other protective measures to prevent any sparks, spatter, or weld splatter from landing on them and potentially contaminating the stainless steel.
Managing Backside Shielding And Purging:
In addition to preventing contamination from external sources, managing backside shielding and purging is crucial when welding stainless steel. Proper shielding and purging can help maintain the quality and strength of the weld. Here are some tips to ensure effective backside shielding and purging:
- Use a shielding gas specifically designed for stainless steel welding, such as argon or a mixture of argon and helium. This gas will create a protective atmosphere around the weld, preventing oxidation and contamination.
- When welding joints with multiple pass welds, consider using backside shielding to protect the back of the weld from oxidation. This can be achieved by using backing bars or copper backing strips.
- For projects that require purging the inside of pipes or tubes, use a purge gas system to displace oxygen and create an inert environment. This will prevent oxidation and maintain the corrosion resistance of the stainless steel weld.
- Monitor the flow rate and coverage of the shielding or purge gas to ensure consistent protection throughout the welding process. Adjust as needed to maintain optimal conditions.
By following these tips for preventing contamination and managing backside shielding and purging, you can ensure high-quality welds when working with stainless steel. Remember, cleanliness and proper gas shielding are essential for achieving strong, durable, and corrosion-resistant welds.
9. Welding Stainless Steel To Different Materials
When it comes to welding stainless steel to different materials, following welding tips is crucial for success. By avoiding common mistakes and using the right techniques, you can achieve high-quality results and ensure a strong and durable weld.
Techniques For Welding Stainless Steel To Different Materials:
When it comes to welding stainless steel to different materials, there are specific techniques that can ensure strong bonds and address the challenges that may arise. Below are some techniques for welding stainless steel to carbon steel, aluminum, and other metals:
- Techniques for Welding Stainless Steel to Carbon Steel:
- Use a filler metal that matches the base metals as closely as possible to achieve a strong bond.
- Employ back-purging techniques to prevent oxidation and ensure proper welding conditions.
- Preheat the carbon steel to reduce the risk of cracking during the welding process.
- Consider using dissimilar filler metals designed for welding stainless steel to carbon steel.
- Techniques for Welding Stainless Steel to Aluminum:
- Use a compatible filler metal specifically designed for welding stainless steel to aluminum.
- Clean the aluminum properly to remove any contaminants and ensure a clean surface for welding.
- Adjust the welding parameters to accommodate the dissimilar melting points of stainless steel and aluminum.
- Avoid excessive heat input that can lead to distortion or warping of the materials.
- Techniques for Welding Stainless Steel to Other Metals:
- Identify the specific metal you are welding stainless steel to and research the recommended techniques for that particular combination.
- Consider using compatible filler metals and adjust the welding parameters accordingly.
- Pre-clean the metals to remove any impurities that may affect the quality of the weld.
- Conduct test welds to determine the optimal settings and techniques for achieving strong and durable bonds.
It is important to note that each combination of materials may require unique approaches and considerations. Therefore, it is crucial to thoroughly research and consult with experts to ensure successful welding outcomes when working with stainless steel and different materials.
10. Post-Weld Cleaning And Finishing
When it comes to welding stainless steel, post-weld cleaning and finishing are critical for achieving optimal results. Follow these tips for effective cleaning and finishing techniques to ensure high-quality welds.
Removing Slag, Spatter, And Other Welding Residues:
- Slag, spatter, and other welding residues can be unsightly and affect the integrity of the weld. To ensure a clean and smooth finish on your stainless steel welds, follow these tips:
- Use a wire brush or stainless steel pickling paste to remove slag and spatter. The brush should be stainless steel to avoid contamination of the stainless steel surface.
- For stubborn residues, you can also use a grinding wheel or abrasive pads to remove them. Be careful not to apply too much pressure, as it can damage the stainless steel surface.
- After removing the residues, clean the welded area thoroughly with a cleaning solution specifically designed for stainless steel. This will remove any remaining contaminants and ensure a clean surface for the next step.
- Use a lint-free cloth or paper towel to dry the cleaned area. Avoid using abrasive materials or brushes that can scratch the stainless steel surface.
- Inspect the weld for any remaining residues or imperfections. If necessary, repeat the cleaning process until you achieve a clean and smooth surface.
- Remember to wear appropriate personal protective equipment, such as gloves and safety glasses, while cleaning the weld.
- Proper post-weld cleaning not only improves the appearance of the weld but also helps maintain the corrosion resistance of stainless steel.
Applying Suitable Finishes To Protect The Stainless Steel:
- Stainless steel is known for its corrosion resistance, but it still requires proper finishing to protect it from environmental factors. Here are some tips for applying suitable finishes to stainless steel welds:
- One commonly used finish is passivation, which involves treating the stainless steel surface with an acid solution to remove contaminants and promote the formation of a protective oxide layer. Passivation can be done through various methods, including immersion in a passivating solution or applying a passivating gel or paste.
- Another option for finishing stainless steel welds is pickling, which involves removing the oxide layer on the surface using a pickling solution. Pickling can be done through immersion or by using a pickling paste or gel.
- Electropolishing is a more advanced finishing technique that combines the benefits of passivation and polishing. It involves applying an electric current to remove a controlled amount of surface material, resulting in a smooth and clean finish.
- For aesthetic purposes, you can also consider painting or powder coating the stainless steel welds. This not only adds color but also provides an additional layer of protection against corrosion.
- Regardless of the finishing method you choose, it’s essential to follow the manufacturer’s instructions and ensure proper surface preparation before applying the finish.
- Regular maintenance and cleaning of the finished stainless steel welds also play a crucial role in maintaining their appearance and corrosion resistance.
11. Preventing Corrosion In Stainless Steel Welds
Preventing corrosion in stainless steel welds is crucial for maintaining the integrity and durability of the welds. Follow these welding tips for stainless steel to ensure long-lasting and corrosion-resistant welds.
Understanding The Causes Of Corrosion In Welded Stainless Steel:
- Exposure to oxygen: When stainless steel is exposed to oxygen, it undergoes a process called oxidation, which can lead to corrosion.
- Contamination: Contamination from other metals, such as carbon steel, during the welding process, can result in galvanic corrosion.
- Heat-affected zones: The heat generated during welding can alter the structure of the stainless steel, creating areas that are more prone to corrosion.
- Chlorides: Stainless steel is particularly susceptible to corrosion in environments with high chloride levels, such as coastal areas or industrial settings.
Implementing Preventive Measures To Ensure Long-Lasting Results:
- Proper cleaning and surface preparation: Thoroughly clean the stainless steel before welding to remove any dirt, grease, or contaminants that could contribute to corrosion.
- Correct welding technique: Use the appropriate welding procedure to minimize the heat input and reduce the formation of heat-affected zones.
- Select the right filler metal: Choose a filler metal specifically designed for welding stainless steel to maintain the corrosion resistance of the material.
- Shielding gas: Utilize a shielding gas, such as argon or a mixture of argon and helium, to protect the weld area from oxidation and minimize the risk of corrosion.
- Post-weld treatment: Apply passivation techniques, such as chemical treatments or electropolishing, to restore the stainless steel’s protective oxide layer and enhance its corrosion resistance.
- Consider the environment: Take into account the operating environment of the welded stainless steel and choose materials and coatings that are resistant to corrosion in that particular setting.
By understanding the causes of corrosion in welded stainless steel and implementing preventive measures, you can ensure long-lasting results and maintain the integrity of your stainless steel welds. Remember to follow proper cleaning and surface preparation procedures, use the correct welding technique, select the appropriate filler metal and shielding gas, and consider post-weld treatment options.
Taking these steps will help protect your stainless steel welds from corrosion and ensure their durability.
12. Common Welding Defects And Troubleshooting
Discover the common welding defects and troubleshooting techniques for welding stainless steel. Enhance your welding skills with these helpful tips to ensure high-quality results.
Identifying Common Welding Defects In Stainless Steel Welding:
- Porosity: Small holes or voids in the weld caused by gas pockets trapped during the welding process.
- Undercutting: Grooves formed along the weld due to excessive heat, resulting in a weak joint.
- Cracking: This occurs when the weld solidifies and contracts, causing stress and fractures in the metal.
- Incomplete fusion: Forges a weak bond between the weld and base metal, reducing strength.
- Burn-through: Excessive heat leads to melting through the base metal, creating a hole or gap.
- Spatter: Small droplets of molten metal that splatter and adhere to the surrounding area.
- Distortion: Warping or bending of the metal due to uneven heating and cooling during welding.
Troubleshooting Tips For Rectifying Defects And Improving Weld Quality:
- Porosity: Increase shielding gas flow rate and use proper cleaning practices to remove contaminants.
- Undercutting: Adjust welding parameters, such as travel speed and current, to reduce heat input.
- Cracking: Preheat base metal, control cooling rate, and use proper welding techniques.
- Incomplete fusion: Increase heat input, improve joint fit-up, and ensure proper electrode angle.
- Burn-through: Use proper welding technique, adjust heat input, and consider using multiple passes.
- Spatter: Maintain correct shielding gas flow and select the appropriate electrode diameter.
- Distortion: Use proper clamping or fixturing techniques to mitigate heat-induced warping.
By understanding common welding defects and implementing troubleshooting techniques, you can ensure high-quality welds when working with stainless steel. Remember to always follow safety guidelines, practice proper technique, and consult with welding experts for specific applications. Happy welding!
13. Safety Precautions For Stainless Steel Welding
When it comes to welding stainless steel, it is crucial to follow safety precautions. These precautions ensure the quality of the weld and protect against potential hazards. By implementing proper safety measures, welders can achieve successful and safe welding outcomes.
Protective Gear And Equipment Requirements For Stainless Steel Welding:
- Welding helmet: A high-quality welding helmet is essential to protect your eyes from harmful radiation and debris. Look for a helmet with a shade level suitable for stainless steel welding.
- Safety glasses: Wear safety glasses under your welding helmet to provide extra eye protection from sparks and flying debris.
- Welding gloves: Invest in welding gloves made of heat-resistant material to protect your hands from burns and sparks.
- Welding jacket or apron: A flame-resistant jacket or apron will protect your torso and arms from sparks and molten metal splatter.
- Welding boots: Wear steel-toed boots to protect your feet from falling objects and hot metal.
- Ear protection: Welding can generate loud noises, so wear earplugs or earmuffs to protect your hearing.
- Respiratory protection: Use a welding respirator or a properly fitted N95 mask to protect yourself from harmful fumes and gases produced during stainless steel welding.
- Fire extinguisher: Keep a fire extinguisher nearby in case of any welding-related fires.
- Welding table or workbench: Use a sturdy welding table or workbench to ensure stability and minimize the risk of accidents.
- Welding clamps: Use clamps to hold the stainless steel pieces securely in place to prevent accidental movement during welding.
Precautions For Working With Potentially Hazardous Substances:
- Ventilation: Ensure that you are working in a well-ventilated area, or use exhaust fans and local exhaust ventilation to remove fumes and gases generated during stainless steel welding.
- Avoid direct skin contact: Minimize direct skin contact with stainless steel surfaces, as they can become hot and cause burns.
- PPE for fume exposure: If you anticipate significant fume exposure, use a powered air-purifying respirator (PAPR) or a supplied air respirator (SAR) to protect yourself from inhaling hazardous substances.
- Proper disposal of waste: Dispose of stainless steel welding waste, such as slag and grinding dust, according to local regulations and guidelines.
- Training and certification: Ensure that you have received proper training and certification in stainless steel welding techniques to minimize the risk of accidents and mishaps.
Remember, safety should always be your top priority when welding stainless steel. Proper gear, equipment, and precautions can help protect you from potential hazards and ensure a safe and successful welding experience.
14. Tips For Welding Thin Stainless Steel Sheets
With these 14 tips for welding thin stainless steel sheets, you can ensure a successful welding process. From adjusting amperage to making tack welds, these guidelines will help you achieve high-quality welds with ease.
Techniques For Minimizing Distortion In Thin Stainless Steel Sheets:
- Use a lower heat input: Lowering the heat input helps prevent overheating and distortion of thin stainless steel sheets.
- Employ the tack welding technique: Tack welding involves creating temporary welds at intervals along the seam to hold the sheets in place before making the final weld. This reduces the chances of distortion.
- Implement intermittent welding: Instead of continuous welding, try intermittent welding by welding in short sections and allowing time for cooling in between. This helps minimize heat buildup and distortion.
- Use a smaller electrode: Choosing a smaller electrode diameter can help control the amount of heat transferred to the thin stainless steel sheets and minimize distortion.
- Utilize a stitch welding technique: Stitch welding involves making a series of short welds along the seam, allowing for cooling between each weld. This reduces the overall heat input and minimizes distortion.
- Consider using a heat sink: Using a heat sink, such as a copper pad or clamp, can help dissipate excess heat and prevent distortion in thin stainless steel sheets.
- Implement controlled preheating: Preheating the sheets to a specific temperature can help reduce thermal stress, minimizing distortion during the welding process.
- Use a backstepping technique: Welding in a backstepping pattern, by welding from the middle towards the edges, can help distribute heat evenly and minimize distortion.
- Avoid excessive weld penetration: Excessive weld penetration can lead to increased heat input and distortion. Adjust welding parameters to control the depth of the weld.
- Ensure proper fit-up: Proper fit-up of the thin stainless steel sheets helps prevent gaps or misalignment, reducing the chances of distortion during welding.
- Opt for a lower welding speed: Reducing the welding speed can help control the heat input and minimize distortion in thin stainless steel sheets.
- Use the correct shielding gas: Choosing the appropriate shielding gas, such as argon or helium, helps create a stable welding environment and minimizes distortion.
- Select the right welding technique: Different welding techniques, such as TIG or MIG, have different heat inputs and characteristics. Choose the technique that best suits your thin stainless steel welding needs.
- Consider using a backing bar or clamp: Using a backing bar or clamp on the underside of the joint provides additional support and helps prevent distortion during welding.
15. Welding Stainless Steel In Different Positions
Welding stainless steel in different positions requires careful techniques and considerations. Learn valuable tips for successfully welding stainless steel in various positions to achieve strong and durable welds.
Welding stainless steel in different positions can present some unique challenges. To achieve high-quality welds, it’s important to use the right techniques and understand the characteristics of the metal. Here are some tips for welding stainless steel in flat, vertical, overhead, and other positions:
Tips For Welding Stainless Steel In Flat, Vertical, Overhead, And Other Positions:
- When welding in the flat position:
- Maintain a steady travel speed and a consistent distance from the workpiece.
- Use a weaving motion to distribute the heat evenly and prevent distortion.
- Be mindful of the angle of the electrode to ensure proper fusion.
- When welding in the vertical position:
- Use a downward welding technique to prevent slag inclusion.
- Control the amperage and travel speed to achieve proper penetration.
- Use smaller diameter electrodes for better control and less heat input.
- When welding in the overhead position:
- Use a smaller electrode diameter to minimize the risk of weld droplets falling.
- Adjust the welding parameters to compensate for gravity and prevent excessive heat buildup.
- Maintain a steady hand and use a whip technique to control the pool.
- When welding in other positions:
- Position the weld joint to allow for easier access and visibility.
- Use the correct electrode angle and travel speed for the specific position.
- Consider using positional fixtures or supports to ensure stability.
Overcoming challenges and achieving quality welds when working with stainless steel requires practice and attention to detail. By following these tips for welding stainless steel in different positions, you can improve your skills and produce strong, durable welds. Remember to always prioritize safety and follow industry best practices for welding stainless steel.
16. Best Practices For Welding Stainless Steel
Unlock the secrets to flawless stainless steel welding with these best practices. From adjusting amperage to choosing the right filler rod, these tips will help you achieve top-notch results.
Applying industry best practices for stainless steel welding:
- Use proper shielding gas: Shielding gas is essential for stainless steel welding as it prevents oxidation and ensures a clean weld. Argon is commonly used as a shielding gas for stainless steel welding.
- Eliminate surface contaminants: Before welding stainless steel, ensure that the surface is clean and free from any contaminants such as oil, grease, or dirt. Use solvents or wire brushes to remove any surface contaminants.
- Preheat if necessary: Some grades of stainless steel may require preheating before welding to minimize the risk of cracking. Check the specifications and preheat if necessary to ensure a successful weld.
- Choose the right filler material: Selecting the appropriate filler material is crucial for stainless steel welding. Match the filler material to the base metal and ensure compatibility for the best welding results.
- Control heat input: Too much heat can negatively affect the mechanical properties of stainless steel. It is important to control the heat input during welding to prevent distortion, warping, or overheating.
- Maintain proper cleanliness: Stainless steel is prone to contamination during welding, which can lead to inferior welds. Keep the welding area clean and use stainless steel brushes dedicated to stainless steel welding to avoid contamination.
- Use proper joint preparation: Different joint designs require different welding techniques. Be sure to prepare the joint properly by following the recommended guidelines for the specific joint type, such as butt joints, T-joints, or lap joints.
- Monitor interpass temperature: Stainless steel welding often involves multiple weld passes. It is crucial to monitor the interpass temperature between each pass to prevent overheating and ensure the weld’s integrity.
- Post-weld treatment: After completing the weld, perform post-weld treatments such as passivation or pickling to remove the heat-affected zone’s impurities and restore the stainless steel’s corrosion resistance.
- Practice weld technique: Stainless steel welding requires skill and practice. Continuously improve your welding skills by practicing different techniques and staying updated with the latest welding resources and technologies.
Remember, following these industry best practices for welding stainless steel will result in high-quality welds and ensure the longevity and integrity of the stainless steel structure.
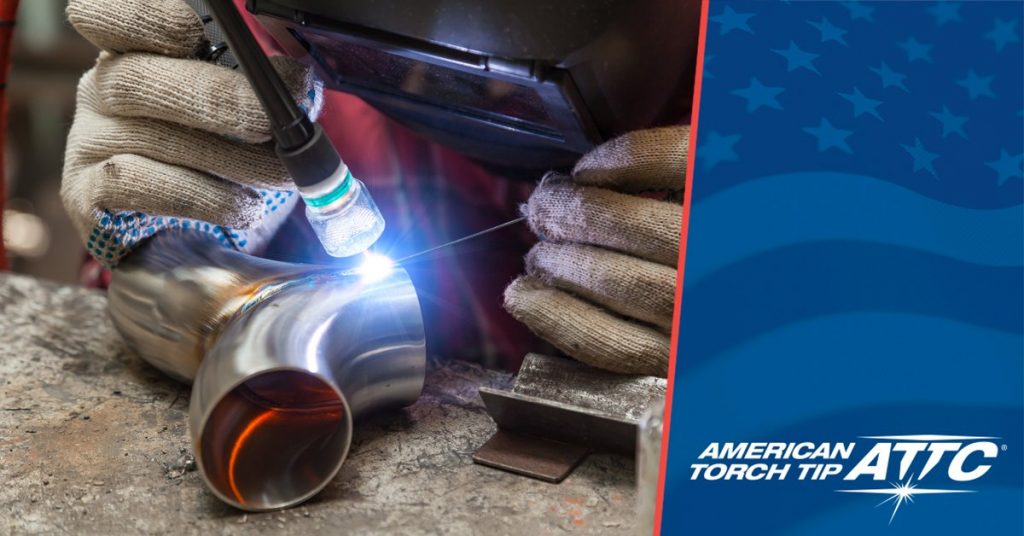
Credit: americantorchtip.com
Frequently Asked Questions Of Welding Tips For Welding Stainless Steel
What Welding Technique Is Best For Stainless Steel?
TIG Welding or Gas Tungsten Arc Welding is the best welding technique for stainless steel. MIG Welding is easier for high-quality work.
What Is The Easiest Way To Weld Stainless Steel?
The easiest way to weld stainless steel is by using Metal Inert Gas (MIG) welding. MIG welding is easier than stick welding and allows for high-quality work with stainless steel.
What Speed Do You Weld Stainless Steel?
The recommended speed for welding stainless steel varies based on the specific application and type of welding process used. It is best to consult welding guidelines or a professional for accurate speed recommendations.
How Do You Prep Stainless Steel For Welding?
To prep stainless steel for welding, follow these steps: 1. Clean the surface thoroughly to remove any dirt, grease, or contaminants. 2. Use a stainless steel wire brush or abrasive pad to remove any oxide layers or discoloration. 3. Degrease the surface with a solvent or alcohol-based cleaner to ensure a clean weld.
4. Finally, use a stainless steel pickling gel or solution to remove any heat tint or scale that may have formed during previous welding or heating processes.
Can You Use Any Welding Technique For Stainless Steel?
Yes, TIG Welding or Gas Tungsten Arc Welding is the best technique for welding stainless steel.
What Are The Tips For Tig Welding Stainless Steel?
Follow these tips for TIG welding stainless steel: adjust the amperage, use a stubby gas lens kit, and properly prepare the surface.
How Do You Prevent Stainless Steel From Losing Its Corrosion Resistance During Welding?
To keep stainless steel stainless, follow the three C’s: Clean the material, Choose the right filler rod, and Control the heat input.
Conclusion
To achieve high-quality welds when working with stainless steel, it is important to follow these essential tips. First and foremost, make sure to use the appropriate welding process. TIG welding, or gas tungsten arc welding, is the most commonly used technique for welding stainless steel due to its versatility and excellent results.
Additionally, proper preparation of the surfaces to be welded is crucial. Thoroughly clean and remove any contaminants or residue before starting the welding process. Another important consideration is to choose the right filler material and adjust the amperage settings accordingly.
Keeping the travel speed consistent and making tack welds at regular intervals can also greatly improve the quality of the welds. Lastly, pay attention to the three C’s: control, cleanliness, and confidence. By ensuring precise control over the welding process, maintaining a clean work environment, and approaching each weld with confidence, you can achieve outstanding results when welding stainless steel.
So, equip yourself with the right knowledge, techniques, and tools, and start mastering the art of stainless steel welding today.