Do Welders Have to Be Strong => Welders need physical strength in their legs and arms, along with good hand-eye coordination, to maintain control of their torch and avoid mistakes. They also spend most of their workday on their feet, so physical stamina is important for the job.
However, welding can be harmful to health if proper precautions are not taken, as it can produce chemicals that can cause skin and respiratory problems. Some individuals may have a natural talent for welding and pick it up quickly, while others may need to practice for an extended period to become proficient.
Along with skill and talent, training, practice, and knowledge of industry trends are important factors for success in a welding career. A steady hand and the ability to perform repetitive work for long periods are also crucial skills for welders.
The Physical Demands Of Welding
Welding is a physically demanding profession that requires individuals to have a certain level of strength and endurance. To excel in this field, welders need to possess physical stamina, arm and hand strength, and hand-eye coordination. Let’s explore each of these aspects in more detail:
Physical stamina and endurance
Welders spend long hours on their feet, constantly maneuvering and operating heavy equipment. As a result, they need to have good physical stamina and endurance to withstand the physical strain that comes with the job. This endurance allows them to maintain focus and precision throughout their workday, ensuring that the welding process is completed with accuracy and efficiency.
Standing for long periods
Standing for extended periods is a common requirement for welders. Whether they are working in a factory, construction site, or fabrication shop, welders need to be able to stay on their feet for the duration of their workday. This requires strength and stability in their legs, allowing them to maintain balance and control while welding.
Arm and hand strength
Another physical demand of welding is the need for strong arm and hand muscles. Welders need to have the strength and control to hold and maneuver heavy welding equipment, such as welding torches and electrodes. This strength allows them to maintain the necessary precision and stability required for accurate welds.
Hand-eye coordination
Welding requires a high level of hand-eye coordination. Welders must be able to carefully guide the welding torch and feed the filler material to create the desired weld. This coordination ensures that the weld is clean and free of defects. Without proper hand-eye coordination, mistakes and inconsistencies can occur, compromising the quality of the weld.
In conclusion, the physical demands of welding require individuals to have physical stamina, arm and hand strength, and hand-eye coordination. By possessing these qualities, welders can perform their job efficiently and effectively, ensuring top-notch welds and contributing to the success of various industries.
The Importance Of Physical Strength In Welding
Do welders have to be strong? Many people wonder about the physical requirements of welding and whether strength plays a crucial role in this profession. While it is true that welding requires a certain level of physical strength, it is not the sole determining factor for success in this field. However, physical strength does have its significance in various aspects of welding.
Controlling the torch
One of the key skills essential for welders is the ability to control the torch. Welders need to have steady and strong arm muscles to maintain control over the torch, ensuring precise and accurate welding. Without adequate physical strength in their arms, welders may face difficulties in maintaining a steady hand, resulting in subpar welds. So, physical strength plays a significant role in achieving high-quality welds.
Avoiding mistakes and slips
Another reason why physical strength is important in welding is to avoid mistakes and slips. Welders spend most of their workday on their feet, requiring good leg strength to stand for long periods. Additionally, hand-eye coordination is crucial to avoid slips and mistakes while operating the welding torch. Welders with strong muscles and coordination are less likely to make errors, ensuring safe and efficient welding processes.
Effectiveness and efficiency
In the welding profession, effectiveness and efficiency are of utmost importance. Physical strength contributes to the effectiveness and efficiency of welders. With strong muscles, welders can maneuver heavy equipment, position bulky materials, and work comfortably in various positions. This enhances their overall productivity and enables them to complete welding tasks efficiently, meeting project deadlines.
In conclusion, while physical strength is not the only determining factor for success in welding, it does play an important role in various aspects. From controlling the torch to avoiding mistakes and ensuring effectiveness, physical strength enhances the quality and efficiency of welding processes. However, it is important to note that with the right training and skill development, individuals can excel in welding, irrespective of their initial physical strength.
The Relationship Between Strong Math Skills And Welding
Math Skills in Welding
Math skills play a crucial role in the field of welding. While many may associate welding with physical strength, the truth is that welders also need to possess strong math skills. Welding involves various measurements and calculations that require accuracy and precision. Whether it’s determining the correct dimensions for a joint, calculating the right amount of material needed, or understanding complex formulas related to heat distribution, strong math skills are essential for welders to perform their job effectively.
Importance of Measurements and Calculations
In welding, accurate measurements and calculations are of utmost importance. Welders need to follow blueprints or specifications provided to them, which often involve detailed measurements. They must be able to interpret these measurements correctly, determine the required angles, and understand geometric principles to create strong and reliable welds. Additionally, calculations are necessary to determine the amount of filler metal, shielding gas, and electrical parameters needed for each welding operation. Being able to perform these calculations accurately ensures that welds are of the highest quality and meet industry standards.
Precision in Welding
Precision is a key aspect of welding. Every weld must be precise and accurate to ensure the structural integrity and safety of the final product. Strong math skills enable welders to understand and execute precise measurements, angles, and calculations needed to create high-quality welds. The ability to measure and calculate accurately allows welders to work with precision and produce welds that are free from defects. Whether it’s fabricating complex metal structures or joining two pieces of material, precision is crucial in every aspect of welding.
The Role Of Work Ethics In The Welding Industry
Ethics and professionalism in welding
Work ethics play a crucial role in the welding industry, where professionalism and ethical behavior are highly valued. Welders, like professionals in any trade, are expected to adhere to a code of conduct that includes honesty, integrity, and respect for the work they do and the people they work with.
Professionalism in welding goes beyond simply knowing how to operate welding equipment and techniques. It extends to how welders approach their work, handle challenges, and interact with colleagues and clients. Adhering to ethical standards ensures that welders maintain a high level of quality and safety in their work.
Importance of strong work ethics
Strong work ethics are essential in the welding industry, as they contribute to a welder’s success and reputation. Welders with strong work ethics demonstrate reliability, accountability, and a commitment to producing high-quality work.
Having a strong work ethic means being punctual, following procedures and protocols, and taking responsibility for one’s work. It involves going above and beyond what is expected, consistently delivering excellent results, and continuously improving one’s skills and knowledge.
Impact on career success
Work ethics have a direct impact on a welder’s career success. Employers value welders who exhibit professionalism, as they can trust them to complete projects on time, meet quality standards, and represent their company well.
Welders with strong work ethics are more likely to be given challenging projects and opportunities for career advancement. Clients and colleagues also appreciate working with professionals who are dedicated, reliable, and ethical in their approach.
Cultivating and maintaining strong work ethics can lead to a fulfilling and prosperous career in the welding industry.
The Qualities And Skills Required To Be A Welder
Welding is a skilled trade that requires a combination of physical abilities and technical knowledge. While strength is certainly beneficial in the field of welding, it is not the sole determining factor for success. In addition to physical strength, welders need to possess hand-eye coordination, knowledge of metallurgy, teamwork, and collaboration skills, as well as problem-solving abilities. Let’s delve into each of these qualities and skills in more detail:
Hand-eye coordination
Hand-eye coordination is crucial for welders as it is essential to accurately guide the torch and control the welding process. A steady hand and precise movement are required to create strong, durable welds. Welders must be able to focus on the area being welded while simultaneously manipulating the torch and filler material. This skill ensures the welder can maintain a consistent weld bead and avoid mistakes or slips that could compromise the quality of the weld.
Metallurgy knowledge
Having a solid understanding of metallurgy is essential for welders. Knowledge of different types of metals, their properties, and how they react to heat is crucial in determining the appropriate welding techniques and settings. Welders need to know which welding processes and materials are suitable for a specific application, as using the wrong combination can result in weak welds, structural failures, and potential safety hazards.
Teamwork and collaboration
Welding is rarely a solo endeavor. Welders often work as part of a team, collaborating with other professionals such as engineers, fabricators, and project managers. Effective communication and teamwork are vital to ensure seamless coordination and successful project completion. Welders must be able to follow directions, work well with others, and adapt to changing circumstances on the job site.
Problem-solving abilities
Welders encounter various challenges during their work, ranging from material inconsistencies to design flaws. The ability to troubleshoot and solve problems on the spot is crucial. Welders must possess critical thinking skills to identify issues, analyze the situation, and determine the best course of action. This includes adjusting welding techniques, selecting appropriate filler materials, or consulting with colleagues or supervisors when necessary.
While physical strength is advantageous in welding, it is clear that welders require a range of qualities and skills beyond sheer muscle power. Hand-eye coordination, metallurgy knowledge, teamwork and collaboration, and problem-solving abilities are all integral to success in the welding profession. By honing these skills, welders can produce high-quality welds, ensure project integrity, and contribute to the overall success of their team and organization.
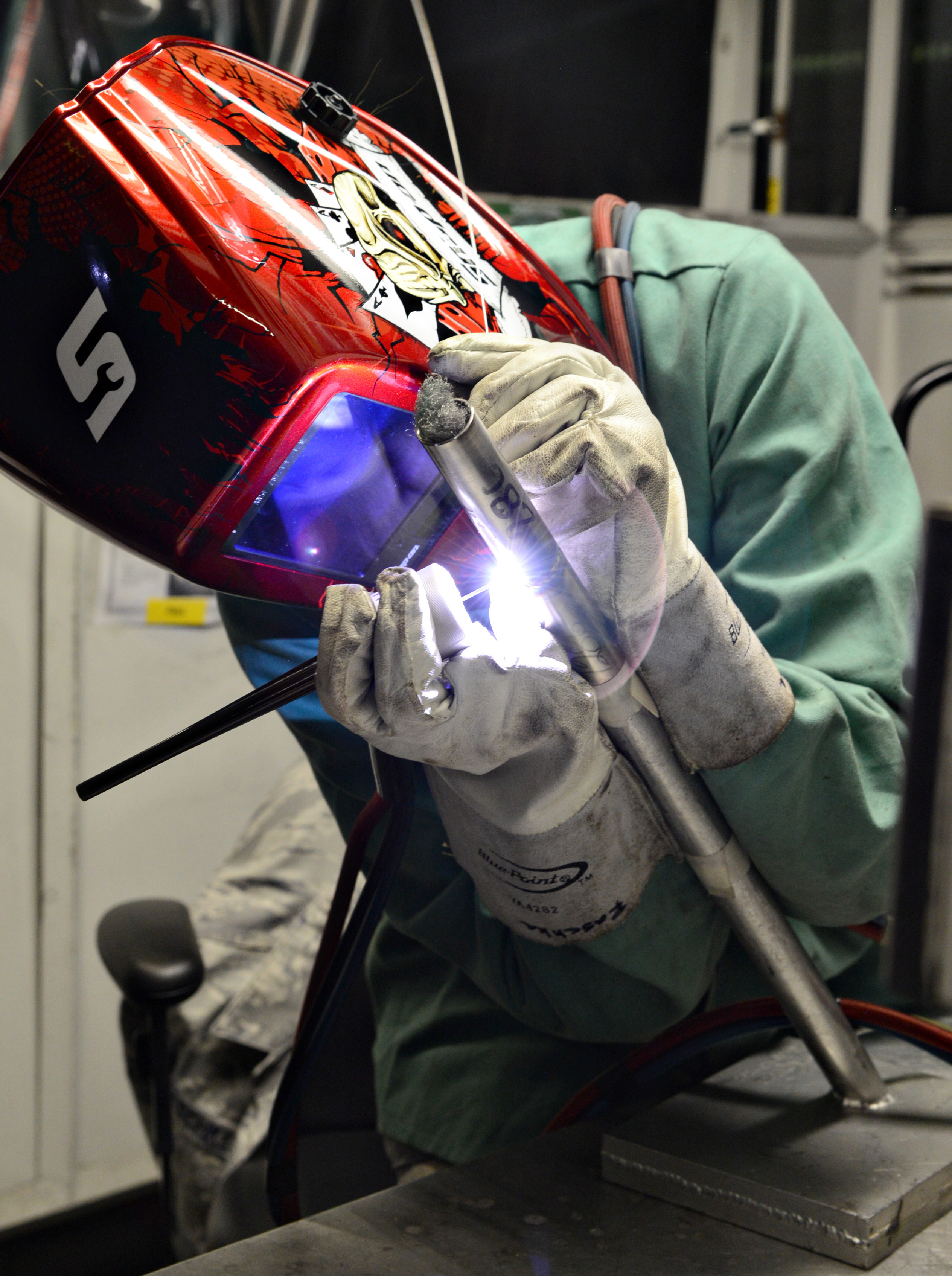
Credit: www.tinker.af.mil
The Impact Of Welding On Health
Risks associated with welding
Welding is a crucial skill in many industries, but it’s important to recognize that it comes with certain risks. One of the main risks associated with welding is the production of harmful chemicals that can have adverse effects on the welder’s health. When metals are heated during the welding process, fumes and gases are released, which can be inhaled and cause respiratory problems. These fumes may contain toxic substances such as nickel, chromium, and manganese, which can lead to lung irritation, asthma, and even more serious conditions like metal fume fever.
Another risk of welding is the potential for skin problems. The intense heat generated during welding can cause burns and other thermal injuries if proper protection is not worn. Additionally, the ultraviolet (UV) and infrared (IR) radiation emitted during welding can damage the skin and eyes. Prolonged exposure to UV radiation can cause sunburn-like symptoms, while IR radiation can penetrate the skin, leading to deep tissue damage. Welders need to use the appropriate personal protective equipment (PPE), such as welding helmets, gloves, and clothing, to minimize the risk of these hazards.
Precautions and safety measures
To ensure the safety and well-being of welders, it is crucial to implement several precautions and safety measures. First and foremost, proper ventilation is essential to remove welding fumes and gases from the work environment. This can be achieved through the use of local exhaust ventilation systems or by working in open-air environments. Employers should also provide adequate training on the hazards of welding and the correct usage of PPE.
Using the right welding technique and equipment is also vital for reducing health risks. For example, using a fume extraction system or wearing a powered air-purifying respirator can significantly decrease the inhalation of welding fumes. Choosing low-fume welding rods and maintaining a safe distance from the welding arc can also help minimize exposure to harmful fumes and radiation.
Skin and respiratory problems
The skin and respiratory system are particularly vulnerable to the hazards of welding. When it comes to skin problems, welders should always wear flame-resistant clothing to protect against burns and sparks. Gloves, aprons, and welding sleeves are also essential to shield the hands, arms, and other exposed areas from heat and molten metal splatter.
Respiratory health can be safeguarded by wearing a respiratory protection device, such as a powered air-purifying respirator (PAPR) or a high-efficiency particulate air (HEPA) filter respirator. These devices can effectively filter out welding fumes and provide clean air for the welder to breathe. It is important to regularly replace filters and cartridges to maintain their efficiency.
Furthermore, welders should undergo regular health check-ups to detect any early signs of respiratory or skin problems. Early detection and treatment can prevent the progression of these conditions and ensure the well-being of the welder.
Overall, welders must prioritize their health and take the necessary precautions to mitigate the risks associated with welding. By implementing proper safety measures, utilizing appropriate PPE, and promoting good ventilation practices, welders can protect themselves from skin and respiratory problems and maintain a healthy work environment.
How To Get Into The Welding Field
Education and Training Options
Getting the right education and training is crucial for entering the welding field. While a formal education is not always required, it can greatly enhance your chances of landing a job and advancing your career. Consider enrolling in a welding program at a technical school or community college. These programs provide hands-on training and cover essential topics such as welding techniques, safety procedures, blueprint reading, and metallurgy. Additionally, some vocational schools offer apprenticeship programs, allowing you to gain practical experience while learning on the job.
Certification and Qualifications
Obtaining proper certification and qualifications is essential for becoming a professional welder. Certification is usually offered by welding organizations or institutions and serves as proof of your skills and competence. The American Welding Society (AWS) is one such organization that provides various certifications, including Certified Welder (CW) and Certified Welding Inspector (CWI). These certifications demonstrate your proficiency in specific welding processes and can significantly improve your job prospects. Additionally, earning relevant qualifications such as becoming a certified pipe welder or an underwater welder can open up even more career opportunities.
Career Opportunities
Once you have the necessary education, training, and certifications, a wide range of career opportunities await you in the welding field. Welders are in demand in industries such as construction, manufacturing, automotive, aerospace, and shipbuilding. You can work for companies, and government agencies, or even start your own welding business. The job outlook for welders is favorable, with a projected growth of 3% from 2018 to 2028, according to the Bureau of Labor Statistics. Moreover, welding skills are transferable, meaning you can easily switch industries or specialize in specific welding processes to broaden your career options and earning potential.
The Salary And Job Outlook For Welders
Average Salary
When it comes to the salary of welders, it can vary depending on factors such as experience, location, and industry. On average, welders can earn a competitive income. According to the Bureau of Labor Statistics, the median annual wage for welders, cutters, solderers, and brazers was $44,190 in May 2020. This means that half of the welders in the United States earned more than this amount, while the other half earned less.
It is important to note that the salary of a welder can increase with experience and additional certifications. Welders who are highly skilled and have expertise in specialized areas such as underwater welding or aerospace welding may also earn higher wages. Additionally, welders who are willing to work in remote or hazardous conditions may also receive higher pay due to the level of risk involved in these jobs.
Job Prospects and Growth
The job prospects for welders are generally favorable, as there is a consistent demand for skilled welders in various industries. Welding plays a vital role in sectors such as construction, manufacturing, automotive, and oil and gas, among others. As new infrastructure projects are undertaken and older structures require maintenance and repair, the need for welders continues to grow.
According to the Bureau of Labor Statistics, the employment of welders, cutters, solderers, and brazers is projected to grow 3 percent from 2019 to 2029. This growth rate is about as fast as the average for all occupations. The demand for welders is driven by factors such as population growth, urbanization, and the need to replace aging infrastructure.
Advancement Opportunities
For welders looking to advance in their careers, there are various opportunities to consider. As welders gain experience and develop their skills, they can take on more complex projects and responsibilities. They may also have the opportunity to specialize in specific types of welding, such as TIG welding or pipe welding, which can open doors to higher-paying positions.
Additionally, pursuing additional certifications and training can greatly enhance advancement opportunities for welders. Certifications from organizations such as the American Welding Society (AWS) can demonstrate expertise and competence in specific welding techniques or industries. These certifications can lead to higher-paying jobs and increased job security.
It’s worth noting that some welders may choose to move into supervisory or management roles, where they can oversee a team of welders and coordinate welding operations. Others may decide to become welding instructors or start their welding businesses.
In conclusion, the salary and job outlook for welders are promising, with competitive wages and growth opportunities available. By continuously updating their skills, pursuing certifications, and gaining experience, welders can unlock a world of possibilities in their career paths.
Frequently Asked Questions On Do Welders Have To Be Strong?
Do You Have To Be Strong For Welding?
No, you don’t have to be strong for welding. Welders need good leg strength for standing and strong arm muscles for torch control. Hand-eye coordination is also important. Welding is not bad for your health if precautions are taken. Some people have a natural talent for welding, but practice is necessary for most.
Can You Be A Healthy Welder?
Yes, you can be a healthy welder as long as you take the necessary precautions. Welding requires physical stamina, good strength in legs and arms, and hand-eye coordination to avoid mistakes. However, there are potential risks associated with welding, such as exposure to harmful chemicals that can cause skin and respiratory problems.
Can You Be Naturally Good At Welding?
Yes, some people have a natural talent for welding, but most people need practice to become proficient. Welding requires good arm strength, hand-eye coordination, and the ability to stand for long periods. Taking precautions is important to protect against health risks associated with welding.
Can Anyone Become A Good Welder?
Becoming a good welder requires training, practice, and knowledge of industry trends and processes. Passion for building and dedication are also essential for a successful career in welding.
Do Welders Have To Be Physically Strong?
Welders need good strength in their legs for standing and steady, strong arm muscles to maintain control of their torch.
Conclusion
Overall, physical strength is important for welders, as they spend long hours on their feet and require steady arm muscles to control their torches. Additionally, hand-eye coordination is crucial to avoid mistakes. However, it is important to note that welding can present health risks if proper precautions are not taken.
With training, practice, and a passion for the craft, anyone can become a successful welder. So, while strength is important, it is not the sole determinant of one’s ability to excel in the welding field.